caTEGORIES
Tags
What Rigorous Testing Do Bolts Suppliers Use for Standard Compliance?
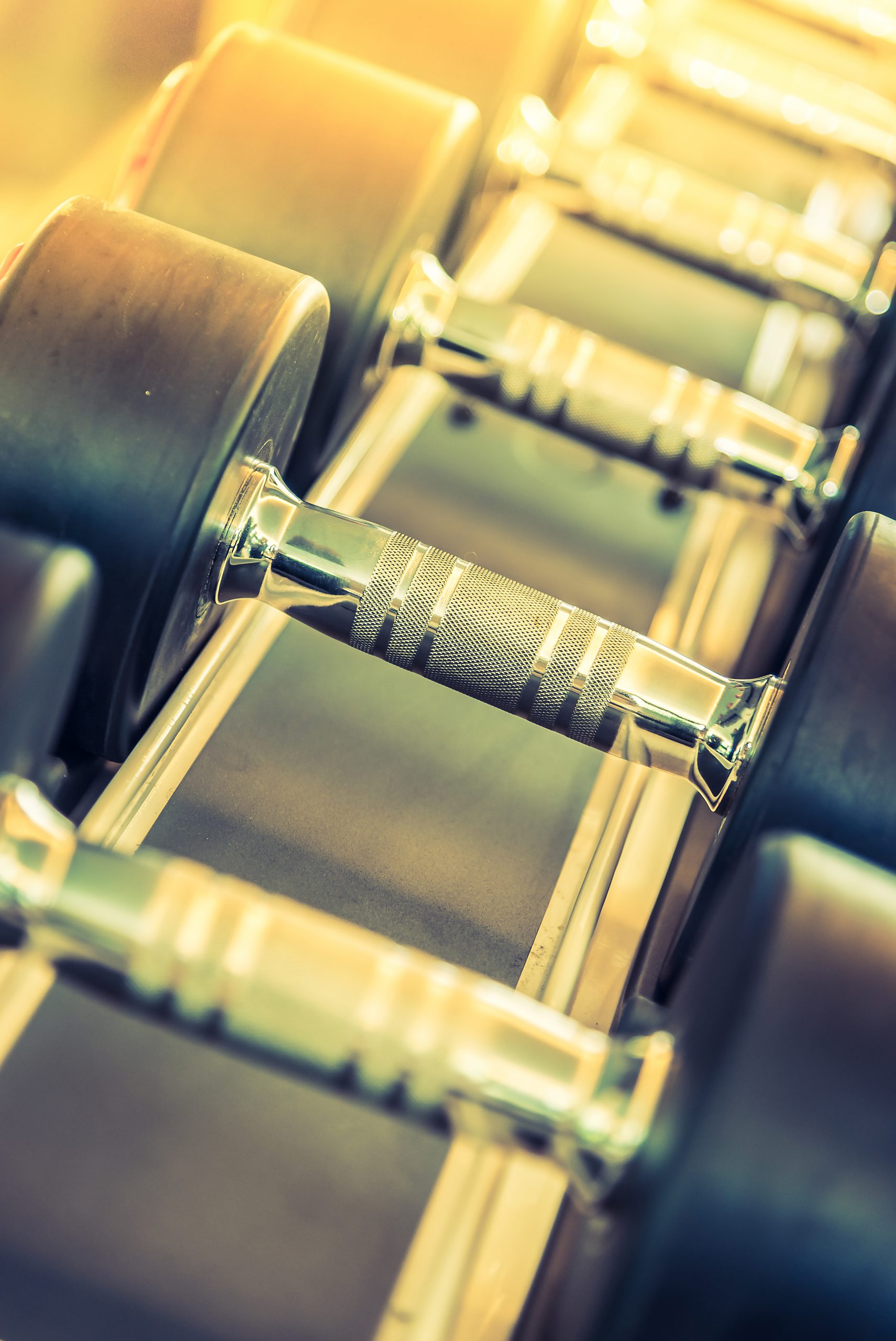
Posted: March 04, 2025
Categories: News
Tags: news
Safety and reliability are paramount when manufacturing bolts, and layers of quality control mechanisms instituted by suppliers, such as through-applicable dimensions and material verification, are critical to ensuring that the process adheres to stringent standards. More complex techniques, like destructive testing, offer extensive analyses of bolt quality. To help establish the quality of the bolts, very sophisticated methods can be used to test the bolts.
Quality Control Measures in Bolt Manufacturing
Importance of Quality Control in Bolts Production
Quality is, of course, exceedingly important for some methods of producing bolts. It is very important to ensure that bolts are proven safe and reliable according to industry standards. Bolts are used in structure construction and machine operation, so any flaw should be fatal. This underscores the need for manufacturers to carefully monitor quality control procedures during the production process.
Common Quality Control Techniques Used by Bolts Suppliers
Manufacturers of bolts apply quality control tools to ensure their products comply with industry standards. They perform visual inspections to detect surface defects or irregularities and dimensional checks to ensure the bolts meet certain dimensions. Material inspections are also performed to check the composition of the bolts to ensure they are made of the intended materials.
Advanced Quality Testing Methods
Non-destructive Testing (NDT) Techniques
A testing facility will help the suppliers locate any defects like hidden flaws or cracks in the bolts which may appear as external defects but are not visible directly with the help of testing methods like testing and magnetic particle inspection, which allows for assessing the quality of bolts without damaging them directly.
Destructive Testing Methods
Testing methods can involve stressing bolts to failure. It comprises tensile strength and hardness tests and impact tests. Some companies do these tests before releasing each lot of bolts for delivery to collect data about the mechanical properties of the bolts and check if they can withstand the real-world forces they are likely to encounter.
Standards and Certifications in the Bolt Industry
Key Industry Standards for Bolts
To ensure the functionality of the bolts in their application and utility, the bolts must be regulated and specified based on the required standards in the industry to maximize their reliability as well as performance level throughout the life cycle. Believed standards, such as DIN 933 for hexagon head set screws or DIN 931 for hexagon head bolts, outline the socket, materials and mechanical properties that screws should comprise. Adhering to these parameters is important for providing consistent and reliable bolting outcomes.
Certification Processes for Bolts Suppliers
Certification processes play an essential role in creating trust between suppliers and consumers by ensuring that every item in the stockpile meets the standards of quality assurance. Some certifications, like 3. I certification follows the guidelines of DIN EN 10204 and shows its commitment to consistently delivering high-quality products.
Technological Innovations in Bolt Testing
Automation and Digitalization in Quality Control
Automation and digital technology have changed how quality control and quality checks have been conducted in bolt manufacturing. Automated inspection systems integrated with cameras and sensors allow for defect detection with high precision. Digitalization also enables the analysis of data in real time. This enables suppliers to precisely monitor production processes in real-time.
Emerging Trends in Bolt Testing Technology
Advanced Materials Analysis
Modern bolt testing technology developments are focused on the analysis of advanced materials with techniques, such as spectroscopy and electron microscopy, providing insights into the material composition on a microscopic level to confirm compliance with current specifications and leverage new materials to enhance overall performance.
Smart Bolts with Embedded Sensors
Sensor-embedded smart bolts are an unprecedented advancement in bolt technology. They can also track stress levels, temperature fluctuations, or imminent failures in real-time, key data for predictive maintenance and enhancing safety across use cases.
Looking for fasteners with guaranteed quality checks? QEWIT provides a selection of products supported by thorough testing protocols and certifications.
Challenges Faced by Bolts Suppliers in Ensuring Compliance
Overcoming Limitations in Current Testing Methods
Bolt suppliers face challenges in complying with industry regulations effectively. One of the significant challenges lies in confronting the limitations of current testing methods. While traditional techniques like tests and dimensional checks are helpful, they may not catch every defect. Some companies use these techniques to evaluate every batch that is shipped. Higher-level strategies (NDT and destructive testing) provide extensive information but require special equipment and expertise. Suppliers will need to strike a balance with these methods to ensure proper quality control.
Balancing Cost and Compliance
Economic Implications of Rigorous Testing
A second challenge is the high cost of testing and the need to ensure that the cost of the bolts being produced meets regulatory requirements. While the implementation of advanced testing methods may be costly and increase bolt prices, the penalties for insufficient compliance are far more severe. Non-adherence can lead to product recalls, liabilities and damage to a supplier’s reputation. This requires suppliers to reconsider their testing strategies to ensure they can distribute products while managing costs.
Recommendations for Choosing a Reliable Bolts Supplier
Evaluating a Supplier’s Commitment to Quality
One of the most important things while making a choice and choosing a supplier for the bolts is to have information about the quality and their standards. Search for suppliers who have experienced quality assurance procedures and certifications such as ISO 9001 or DIN EN 10204 3. These certifications demonstrate the supplier’s commitment to quality standards and ensuring the availability of quality products.
Leveraging QEWIT Products for Enhanced Compliance
Advantages of Partnering with QEWIT as a Supplier
There are numerous advantages to partnering with QEWIT when it comes to fulfilling the requirements of the meeting industry. This company started pretty strong in 2004, establishing itself as a reliable provider of premium quality fasteners and fixtures throughout Europe and the rest of the world. Its vision is to become the world’s largest supplier of fully modular data center infrastructure products. With more than 30,000 product choices available, QEWIT simplifies how you purchase your product from one source, expediting operations while reducing costs.
QEWIT is committed to assuring the best quality, and the various testing methods used include nondestructive and destructive ones. In addition, they provide customized ISIR as well as PPAP up to level 3 when required.
Apart from this, QEWIT provides tailor-fastening products to make specific products meet customers’ requirements exactly. They are well-equipped with customer service and the account manager provides a sophisticated service. They ensure technical support and also the rapid manufacturing process
In conclusion, the selection process for a provider of bolts involves determining their commitment to excellence through certification, verification, process and customer care. As a quality partner with an enviable focus on compliance and innovation in bolt production, QEWIT ensures that your initiatives are supported by high-class fasteners that comply with laid-down industry standards.