caTEGORIES
Tags
Understanding Drill Screws: Types and Applications in Metalwork
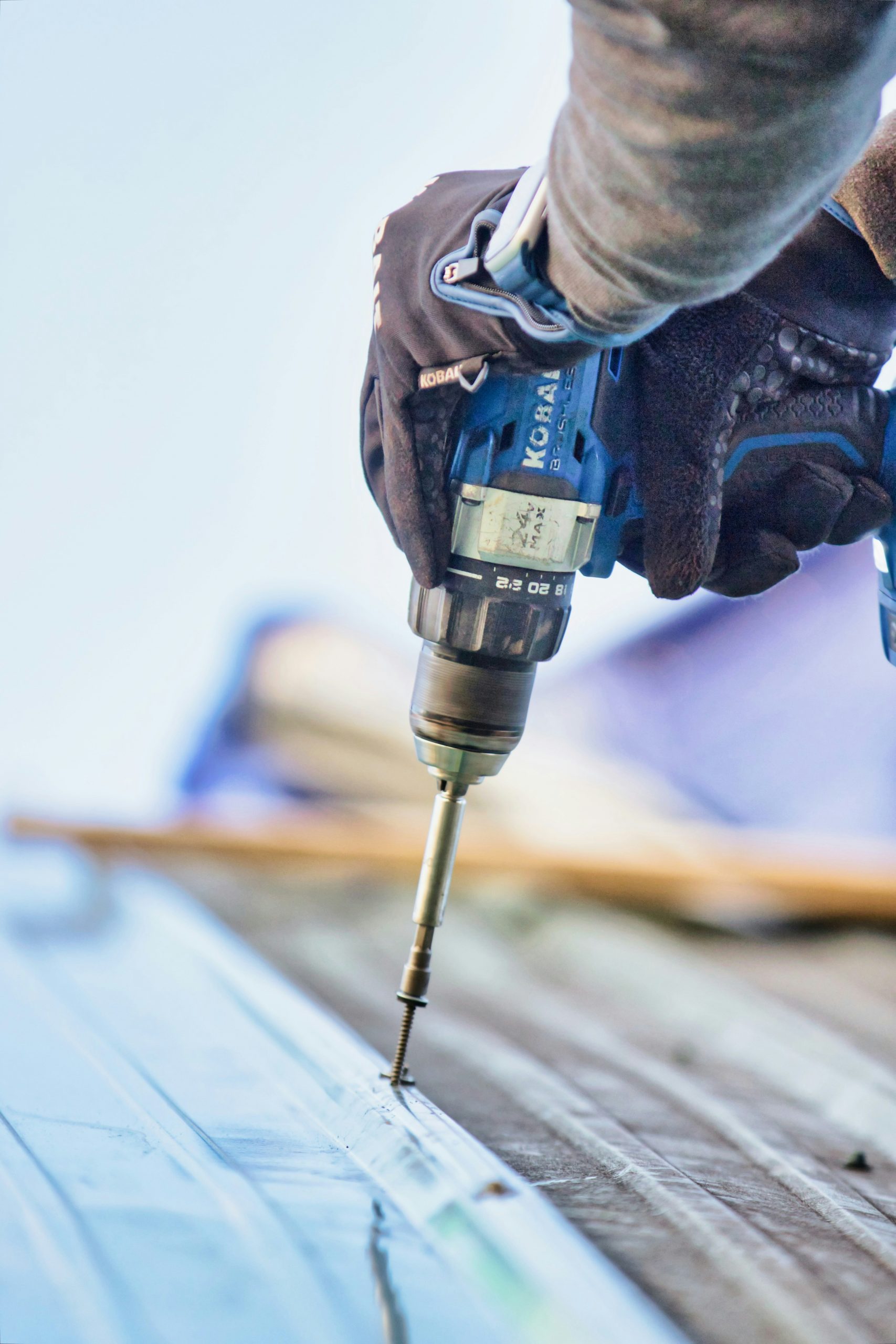
Posted: December 31, 2024
Categories: News
Drill screws are essential in metalworking as they combine drilling and fastening tasks into one operation, providing efficiency and a strong connection between parts. These screws have evolved over time to meet the requirements of engineering and construction practices. QEWIT offers a range of dependable and customized drill screws for various applications. Proper installation techniques, including surface preparation, drilling, and securing, ensure optimal performance.
Overview of Drill Screws in Metalwork
Definition and Functionality
Screws used for drilling are crucial in metalworking as they streamline the process by combining drilling and fastening tasks into an operation seamlessly. They have a tip that acts as a drill bit to penetrate materials without pre-drilling requirements. This unique design boosts efficiency, guaranteeing a strong and long lasting connection between parts. These screws are highly appreciated in projects that demand accuracy and quick execution.
Historical Development
The development of drill screws has progressed due to the requirements of engineering and construction practices. These screws were first created to improve upon the shortcomings of fasteners and have gone through substantial enhancements. From their forms in the early days of industrial use to the highly specialized varieties, drill screws have continuously evolved to cater to various industries. Innovations like material compositions, more advanced coatings and improved tip designs have strengthened their position in metalworking.
Types of Drill Screws
Self-Tapping vs. Self-Drilling Screws
When you’re choosing drill screws for your project or task at hand, it’s important to know the difference between self tapping and self drilling varieties. Self tapping screws are designed to be used with a drilled hole making them suitable for softer materials or situations where precise alignment is key. On the other hand, self drilling screws come equipped with their own drill point removing the need for any pre-drilling. These types are best suited for materials, like steel or aluminum providing both ease of use and robustness in construction projects.
Specialty Drill Screws for Specific Applications
Drill screws designed for industries come in various specialized versions to meet unique needs – like those with high heat resistance for extreme conditions or ones with sealing washers to prevent leaks in roofing projects – ensuring that every job gets the right solution.
Applications of Drill Screws in Metalwork
Industrial Uses
In factories and workshops, screwdrivers are essential for putting machinery together and keeping equipment in condition. They’re crucial for holding tough materials firmly without weakening the structure in manufacturing sites and production units.
Construction and Infrastructure Projects
In the world of construction projects, drill screws play a role in tasks ranging from framing to roofing installations. They are tools that can be used with different materials such as steel beams, aluminum panels and composite structures. The importance of their efficiency in large scale infrastructure projects cannot be emphasized enough.
Automotive and Aerospace Industries
Industries like aerospace industries require screws that can meet strict safety standards and remain lightweight at the same time for various applications, such as building vehicle frames or securing parts of airplanes to ensure durability in harsh conditions.
For individuals, in fields looking for top-notch solutions that cater to their unique requirements, QEWIT delivers exceptional performance and dependability in all the mentioned areas of use.
Selecting the Right Drill Screw for Your Project
Material Composition and Coatings
The performance and durability of drill screws are greatly influenced by the materials they are made of – stainless steel or carbon steel among others – which are chosen for their ability to withstand different environmental factors like corrosion resistance and moisture exposure coatings such as zinc plating or epoxy finishes add an extra layer of protection that makes these fasteners ideal for outdoor or high moisture settings.
Factors to Consider
When selecting drill screws for your projects needs, it’s crucial to assess important aspects. You should take into account the type of material you’re working with. Different materials call for screw varieties to guarantee maximum effectiveness and longevity. For instance, self drilling screws are perfect for metals such as steel or aluminum; whereas self tapping screws might be more suitable for softer materials.
Evaluate the factors of your project. If the task involves moisture or corrosive substances choosing screws with coatings, like zinc plating or epoxy finishes can help prolong their lifespan. Also make sure that the screws size and length match the thickness of the materials being attached to prevent any vulnerabilities.
Consider any needs your project might have to address unique challenges—for example, ensuring excellent water resistance, for roofing installations or prioritizing heat tolerance in industrial environments—choosing specialized drill screws tailored for these applications can lead to more effective outcomes.
Recommendations from QEWIT Products
QEWIT provides a range of options for professionals looking for dependable solutions that are customized for different uses and adhere to industry norms. They offer products that cater to a variety of requirements. From fasteners, to specialized choices tailored for challenging conditions. QEWIT is dedicated to maintaining standards of quality and creativity in all its products to guarantee top-notch performance every time.
Installation Techniques for Optimal Performance
Tools and Equipment Required
To effectively install drill screws, you’ll need the tools and equipment on hand. Having a power drill with torque settings is crucial for maintaining precision while working on the installation process. Make sure to use drill bits and screwdriver attachments that are compatible with each other to ensure a fit between the tool and screw head. Don’t forget to wear safety gear, like gloves and goggles to protect yourself from any risks while operating the equipment.
Step-by-Step Installation Guide
Preparing the Surface
Ensuring that the surface is properly prepared is essential for creating a connection between materials. Start by cleaning the surface to eliminate any dirt, oil or particles that might hinder the screws hold. Using a rust inhibitor can help boost longevity when dealing with metal surfaces vulnerable to rust or corrosion.
Drilling Process
Place the tip of the screw where you want it on the material making sure it’s up and down to avoid any issues when drilling begins. Start your power drill at a speed and keep pushing steadily until the screw goes all the way into the material.
Securing the Screw
Insert the screw into position and secure it in place properly by adjusting the torque settings on your power drill to avoid over-driving it. If not, both the screw and the material its being drilled into could potentially harmed. Check that each screw is either level with or slightly below the surface for a final look.
Maintenance and Longevity of Drill Screws
Regular Inspection Protocols
Regular checks are essential for keeping drill screws in condition in the long run by spotting any signs of wear or damage early on – like rust or bending – that might affect how well they work; fixing these problems right away helps stop them from getting worse over time.
Best Practices for Extending Lifespan
Make sure to store any drill screws properly to maintain their quality for future use. Keep them in a place away from moisture and extreme temperatures that could lead to corrosion or weaken the materials.
Applying lubrication periodically can minimize friction during installation and reduce wear both on screws and tools. Use suitable lubricants designed specifically for metal fasteners to ensure compatibility without affecting performance.
By following these guidelines and utilizing high-quality products like those offered by QEWIT, you can achieve long-lasting results in your metalworking projects while maximizing efficiency and reliability at every stage of application.