caTEGORIES
Tags
Stop Wasting Time! The Engineer’s Guide to Flawless Pin Alignment in 3 Steps
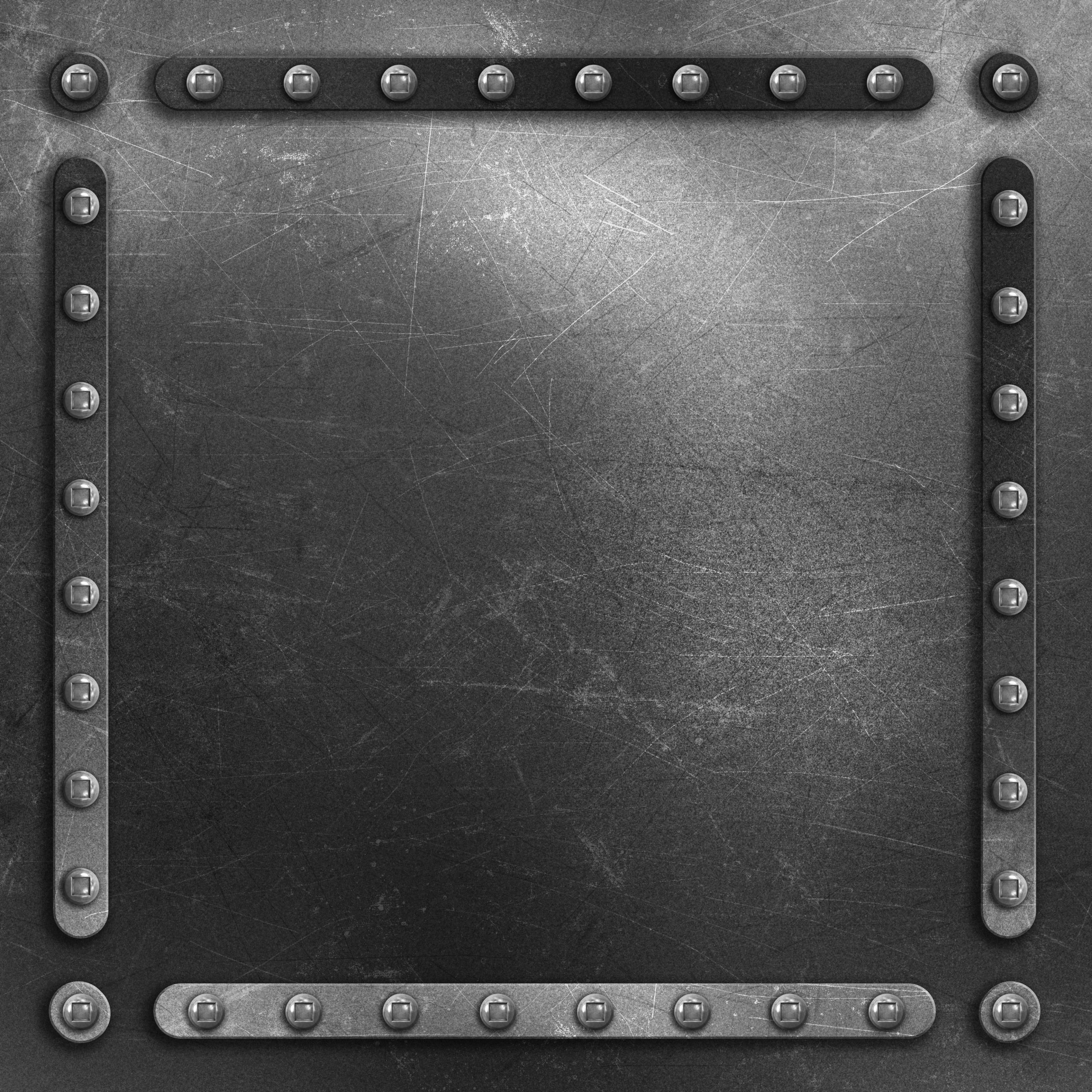
Posted: March 18, 2025
Categories: News
Tags: news
Pin positioning is a vital element in assembly, guaranteeing the correct linkage and steadiness of parts. In segmental construction techniques, such as span-by-span and T-symmetrical approaches, accurate pin placement is highly important. It’s critical to position round pins precisely to secure a tight and exact fit. This precision ensures components are properly located and oriented, avoiding potential problems or offsets during assembly. Effective pin positioning is essential for preserving the structural strength and operational quality of the final product.
Understanding the Significance of Pin Positioning in Assembly
The Function of Pins in Mechanical Structures
Pins are key elements in mechanical setups, acting as essential pieces for positioning, securing, and maintaining structural solidity. They deliver accurate placement and reinforcement for different sections, enhancing the system’s overall performance and longevity. Proper use of pins greatly improves the dependability and efficiency of mechanical frameworks.
Typical Obstacles in Pin Positioning
Securing accurate pin placement can be tricky due to multiple reasons. Differences in part tolerances, heat-related expansion, and misunderstandings during planning can create alignment difficulties. These issues often lead to longer assembly durations, increased expenses, and possible mechanical breakdowns if not resolved quickly.
Effects of Misplacement on Assembly Efficiency
Incorrect pin positioning can seriously harm assembly effectiveness. It might result in excessive wear on parts, causing early breakdowns. Moreover, misplaced pins can weaken the assembly’s structural soundness, posing safety risks or lowering operational performance. Thus, ensuring precise pin placement is vital for sustaining top efficiency and durability in mechanical systems.
Step-by-Step Instructions for Perfect Pin Positioning
The detailed instructions for achieving perfect pin positioning stress the need for exact placement and adjustment. Accurate alignment is crucial for safely managing key components. The guide underscores the importance of verifying proper positioning and steering clear of common mistakes that could disrupt the process. It also highlights selecting the ideal needle for specific tasks and using tools like pliers for the shimmy technique. Following these outlined steps helps achieve impeccable pin positioning and improves pump balance and alignment effectively.
Choosing the Appropriate Pins for Your Assembly
Evaluating Material and Dimensions
When picking pins for your assembly, evaluating the material and size suited to your needs is critical. Pins crafted from materials like carbon steel, stainless steel, or brass provide different levels of durability and rust resistance. The dimensions must match other parts to ensure a firm fit without undue strain or distortion.
Matching with Other Parts
Ensuring compatibility with other components is crucial when selecting pins. Verify that the chosen pins correspond to the measurements and requirements of connecting pieces to avoid alignment problems. This step helps uphold the structural stability and performance of the entire setup.
Methods for Exact Pin Placement
Equipment for Precise Positioning
Using the right tools and gear is essential for precise pin placement. High-accuracy devices like gauges, alignment fixtures, and custom jigs assist in correct positioning during assembly tasks. These instruments reduce mistakes and deliver uniform outcomes across various assemblies.
Top Practices for Manual and Machine-Driven Methods
Whether using manual or automated methods, sticking to best practices is key for perfect pin positioning. In manual tasks, close attention to detail during measurement and placement prevents errors. For automated systems, programming precision equipment with correct data ensures consistency and minimizes human mistakes.
Maintaining Uniformity and Quality Assurance
Techniques for Inspection and Confirmation
Applying strict inspection methods is vital for confirming pin positioning accuracy. Approaches like visual checks, size verification with calipers or micrometers, and non-invasive testing help spot potential misplacements before completing assemblies.
Using Feedback Mechanisms for Ongoing Enhancement
Setting up feedback mechanisms enables constant oversight and refinement of pin positioning processes. Gathering data from test outcomes offers insights into areas needing improvement. Leveraging this data promotes a culture of ongoing progress in manufacturing activities.
For top-notch fasteners, including pins, consider exploring products known for outstanding reliability in assembly applications.
Utilizing QEWIT Solutions for Improved Pin Positioning
Summary of QEWIT’s Cutting-Edge Offerings for Engineers
QEWIT is celebrated for its wide array of premium fasteners and fixings, providing innovative options for engineers aiming for dependable pin positioning in assembly tasks. The company’s dedication to quality shines through its varied product lineup, including threaded inserts, bolts, screws, nuts, washers, and beyond. These items are made from high-grade materials like carbon steel, stainless steel, brass, and alloys, ensuring toughness and corrosion resistance.
QEWIT offers a broad range of fasteners designed to meet diverse application demands. Whether you need standard-grade fasteners or specialized items made from brass or stainless steel, QEWIT has the know-how and resources to deliver top-tier quality. Their focus on customer satisfaction shows in their thorough quality checks and ability to provide traceable test certificates.
By opting for QEWIT products, engineers gain access to technical guidance, custom solutions, and exceptional support. The company blends a “Western Style” business approach with “Far Eastern Value,” making it a reliable ally for superior pin positioning solutions.
How QEWIT Equipment Supports Precise Pin Positioning
QEWIT’s tools are engineered to aid accurate pin positioning with features that boost precision and efficiency in assembly tasks. Advanced equipment like vision measurement projectors and tensile strength testers ensures every product meets strict quality benchmarks before shipping.
The company’s innovation includes non-standard product services, and crafting custom fastening solutions based on customer specifications or samples. This flexibility allows engineers to achieve perfect pin positioning with tailored components that seamlessly fit their assemblies.
Additionally, QEWIT provides various plating options like black oxide, bright zinc, and hot-dipped galvanization. These finishes enhance both appearance and protection against environmental factors that might affect pin positioning over time.
Real-Life Examples and Achievements with QEWIT Products
Engineers in industries like automotive, aerospace, and construction have successfully used QEWIT products to optimize pin positioning in their assemblies. QEWIT’s fasteners have helped overcome typical alignment challenges and boost overall assembly performance.
One success story features hexagon head set screws meeting standards like DIN 933 and ISO 4017. Made from high-tensile steel with a hexagon drive, these screws have a bright zinc-plated finish for enhanced rust resistance—key for maintaining pin positioning over time.
In another case, nylon insert nuts per DIN 985 offered a cost-effective way to prevent loosening from vibration, a frequent assembly issue. The nylon neck grips threads tightly when secured, ensuring firm fastening without sacrificing alignment precision.
For those eager to explore these advanced solutions or need specific fasteners like hexagon head bolts, QEWIT is a dependable partner for flawless pin positioning every time.
FAQs
Q1: How do I pick the best finish for my pins?
A: Assess environmental conditions like moisture or chemical exposure; finishes like bright zinc plating provide excellent rust protection.
Q2: What advantages do non-standard products offer?
A: They enable customization to match unique design needs, ensuring ideal fit and structural strength in assemblies.
Q3: Why is quality assurance critical in pin positioning?
A: It guarantees consistency across production runs, reduces errors during assembly, and boosts product reliability through thorough testing.