caTEGORIES
Tags
Smart Techniques to Eliminate Self Tapper Installation Errors
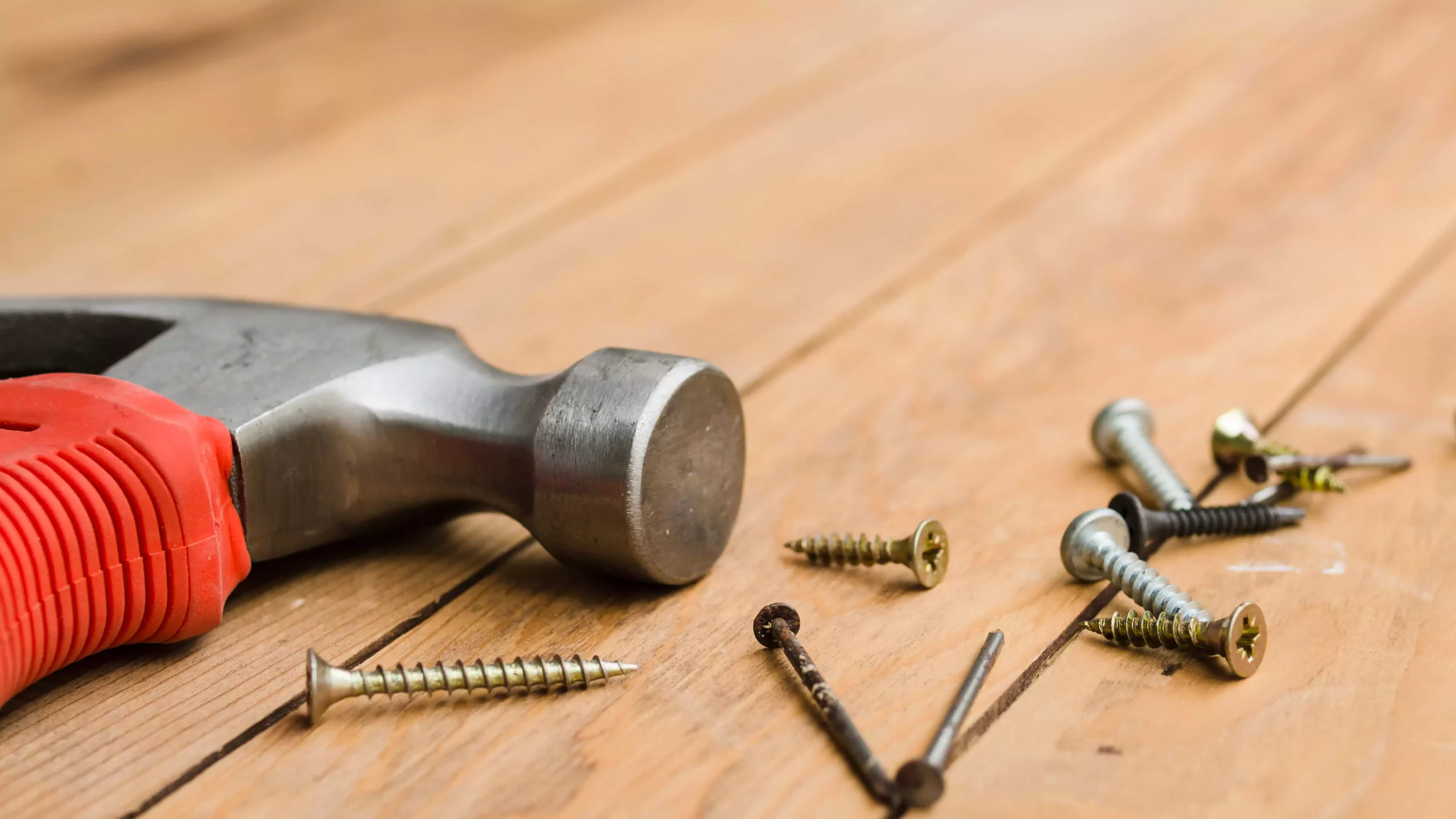
Posted: August 22, 2024
Categories: News
Self-tapping screws, commonly referred to as self tappers, have become essential tools in various applications requiring quick and efficient installation. However, despite their convenience, installation errors are prevalent and can compromise the integrity of the assembly. Understanding common mistakes associated with self-tapper installation can significantly improve the process and lead to better outcomes. This article explores these common installation errors and offers smart techniques to mitigate them.
What Common Mistakes Do People Make with Self-Tappers?
Choosing the Wrong Size or Type of Self-Tapper
One common mistake made during installation is selecting the incorrect size or type of self-tapper. It’s crucial to match the specific requirements of the project with the characteristics of the self-tapper, such as diameter, length, and thread type. Using a self-tapper that is too short or too thin can lead to insufficient grip, resulting in a weak connection. On the other hand, a self-tapper that is too large may cause damage to the material or fail to penetrate effectively.
To avoid this mistake, do thorough research on the materials being used and consult manufacturer specifications. It’s also wise to have a range of sizes available to ensure the appropriate match for the job. When selecting a self-tapper, consider factors such as material type—whether it’s carbon steel or stainless steel—and the specific finish, like bright zinc plated, which affects corrosion resistance.
Failure to Pre-Drill Holes When Necessary
Another frequent error is failing to pre-drill holes when necessary. Pre-drilling is not always mandatory, but in some cases, it can significantly affect the performance of the self-tapper. For instance, when working with particularly hard materials or thicker surfaces, skipping the pre-drilling step can lead to stripped threads or breakage of the screw.
Understanding when pre-drilling is required allows for better installation outcomes. For example, materials like metal might benefit from pre-drilled holes to ensure a snug fit and minimize resistance during installation. To accurately pre-drill holes, select a drill bit size that corresponds with the core diameter of the self-tapper. This practice ensures a perfect fit while allowing the self-tapper to perform effectively.
Not Aligning Screws Correctly
Misalignment of self-tappers during installation is a common issue that can lead to structural problems. When screws are not aligned correctly, it may contribute to uneven load distribution, risking failure of the joint or revealing gaps that undermine the integrity of the assembly.
To mitigate misalignment errors, it is important to establish a clear guideline or mark where the self-tappers will go. Use clamps or jigs as needed to hold materials in place and ensure everything is lined up correctly before beginning the installation. Checking the alignment frequently during application helps to ensure accuracy and can prevent costly errors.
Using Incorrect Torque Settings
Using incorrect torque settings when installing self-tappers can have detrimental effects on the installation. Over-tightening can strip threads or even break screws, while under-tightening may lead to loosening over time. It’s essential to achieve a balance that secures the screw without causing harm to the material or the thread structure of the self-tapper itself.
Establishing guidelines for adjusting torque settings is crucial. Use a torque wrench to ensure the specified torque is applied accurately. Understanding the specific requirements for the self-tappers being used, including factors such as the material and thickness being fastened, is vital in determining the suitable torque settings.
How Can You Ensure a Better Installation Process?
Qewit Self Tapping Screws
Using high-quality products like Qewit self-tapping screws can significantly improve the installation process. The Pan Head Self Tapping Screws DIN 7981C and Self Tapping Drilling Screws DIN 7982F are ideal for many applications due to their robust construction and efficient design. These screws are available in various sizes and materials, allowing for versatility in different installation situations.
The appropriate self-tapping screw ensures optimum performance and reliability. The standard specifications for sizes ranging from ST2.2 to ST6.3 and lengths between 4.5 to 50mm cover a broad spectrum of use cases. Their bright zinc plating enhances corrosion resistance, making them suitable for both indoor and outdoor applications.
Utilizing Quality Tools and Equipment
Quality tools and equipment are fundamental to effective self-tapper installation. Essential tools include screwdrivers, drills, torque wrenches, and clamps. Utilizing reliable tools ensures accurate drilling and tightening, reducing the likelihood of errors that stem from improper technique.
Investing in good equipment pays off by enhancing efficiency and longevity in projects. Proper tools not only help streamline the installation process, but they also contribute to achieving clean and precise results without unnecessary damage to materials.
Practicing Proper Technique
Proper technique is core to a successful self-tapper installation process. A step-by-step guide can be beneficial, including steps such as verifying alignment, pre-drilling when required, and applying the correct torque settings. Taking the time to follow each step carefully can prevent many of the common mistakes associated with self-tapper installations.
Equally important is knowing what practices to avoid during installation. Rushing through the process, using inferior screws, or neglecting tool maintenance can all lead to installation failures. Focusing on a methodical approach can lead to improved outcomes and reduced rework.
Regular Inspection and Maintenance
Lastly, regular inspection and maintenance are essential for long-term joint integrity after installation. Performing routine checks ensures that any issues arising from loosened screws or misalignment can be identified early. This proactive approach helps remedy problems before they escalate into significant failures.
Identifying and fixing these issues early can significantly impact the durability of the assembly. It allows for timely adjustments, ensuring that the installation continues to function as intended, contributing to the durability of the overall project.
Best Practices for Preventing Future Errors
Keeping a Comprehensive Checklist
Having a comprehensive checklist is a smart technique to prevent errors during self-tapper installation. Checklists serve as a reminder for all critical steps involved in the installation process, ensuring nothing is overlooked. This includes verifying the size and type of self-tapper, confirming the need for pre-drilled holes, and checking alignment before securing the screws. Moreover, documenting the tools and materials required helps in organizing the workspace effectively, reducing the time spent searching for items mid-project.
Items to Include in Your Checklist
To create an effective checklist, certain key items should be included. Begin with a review of the project specifications to confirm the required self-tapper size and type, such as the DIN 7982F countersunk self-tapping screws or DIN 7981C pan head self-tapping screws, specifying their dimensions and materials—carbon steel or stainless steel. Next, ensure that the tools for installation are readily available, such as the appropriate drill bits, screwdrivers, and torque wrenches. Additionally, include checks for alignment markers on the material surface and verify that pre-drilling is performed if necessary.
Advantages of Using Checklists
The advantages of using checklists are manifold. Primarily, they maximize efficiency by streamlining the installation process and minimizing distractions. A well-structured checklist fosters accountability by clearly outlining individual responsibilities during installation, which can be particularly beneficial in team environments. Furthermore, checklists also contribute to improved safety practices by reminding installers of essential precautions, like wearing appropriate personal protective equipment (PPE) and conducting a thorough inspection of the work environment.
Continuous Education and Training
Continuous education and training are essential components of mastering self-tapper installation techniques. Staying updated with the latest industry practices not only keeps individuals informed but also empowers them to share knowledge within their teams. Regular training on equipment usage, recent advancements in self-tapper technology, and updated standards can markedly reduce mistakes during installation. Engaging in workshops or webinars focused on installation techniques can also provide hands-on experience, enhancing understanding and efficiency.
Opportunities for Skill Development
There are numerous opportunities for skill development in the field of self-tapper installation. Participating in manufacturer-sponsored training programs often provides detailed calls on specific screws, including technical specifications and best application practices. Additionally, online courses covering various aspects of construction and fastener technology allow for flexible learning at one’s own pace. Another option is on-the-job training, where experienced installers can provide mentorship to newcomers, sharing valuable insights based on real-world experiences and challenges encountered during installations.
Resources for Staying Updated with Best Practices
Utilizing available resources allows individuals to stay informed about best practices in the industry. Subscribing to relevant trade publications can provide insight into new tools and methods, while online forums and discussion groups offer a platform for peer-to-peer knowledge sharing. Attending trade shows and exhibitions also presents opportunities to engage with industry leaders and explore innovative products firsthand. Furthermore, many manufacturers publish technical documents and installation guides that can serve as excellent references when enhancing installation skills with self-tappers.