caTEGORIES
Tags
Sharp Decisions: How Drill Point Design Impacts Drill Screw Performance?
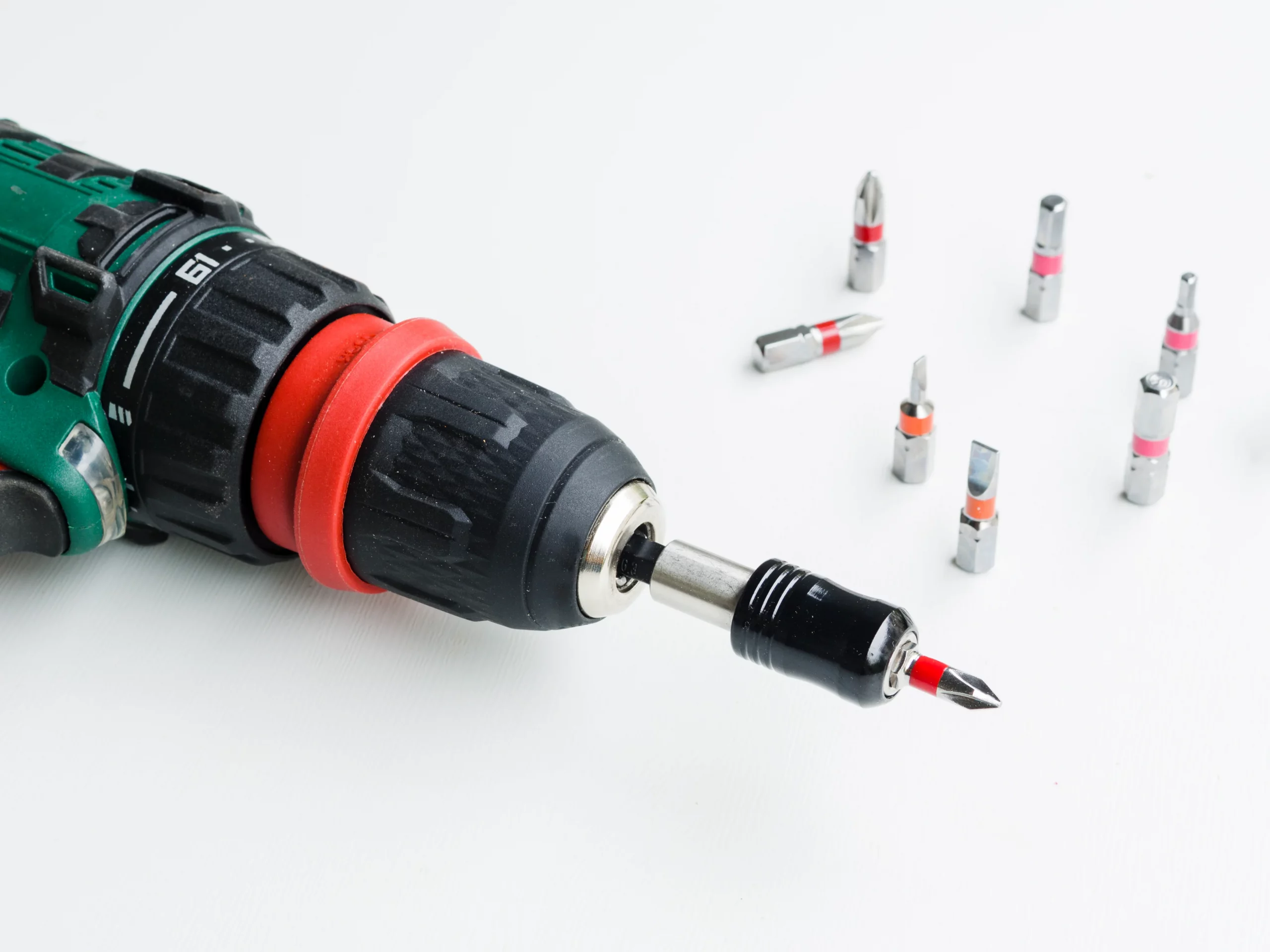
Posted: December 05, 2024
Categories: News
Drill screws are a tool that can be seen in workshops and construction sites worldwide. Their capacity to drill, tap, and secure in a fluid motion saves both time and energy y. This makes them popular among both professionals and those who enjoy do-it-yourself projects. Behind the facade of this tool lies a realm of intricate design details which especially impact its effectiveness across different materials.
What are Drill Screws?
Drill screws get their name from having a drill bit at the tip to make pilot holes as they are screwed in without the need for pre-drilling, like regular screws do.
Drill Screws: A Combined Solution
The drill screws strength lies in its capacity to carry out tasks simultaneously; when you exert force to rotate it and drill a hole into the material with its tip while also securing the screw in place by engaging its threads with the hole it creates—a drilling and tapping process that distinguishes drill screws and makes them suitable for diverse uses.
What are Drill Points?
The tip of a drill screw plays a role in how it works with various materials as different designs are tailored to perform best based on specific applications and material characteristics.
The Importance of Drill Point Design
Selecting the type of drill bit is crucial as it can determine whether your installation goes smoothly or turns into a possibly harmful process. Using a drill bit can result in issues such as:
Binding and breakage: If the screw threads engage with the material before the pilot hole is completely drilled, the drill screw can bind, leading to increased torque and potential breakage. This is especially problematic when working with harder materials.
Overheating: The friction generated during drilling produces heat. If the drill point is not designed to effectively clear the chips created during drilling, they can accumulate around the point, trapping heat and potentially causing the point to overheat and fail. This can lead to dulling of the point or even breakage.
Poor holding power: An unsuitable drill point might not create a secure enough hold in the material. This can result in the screw loosening over time, compromising the structural integrity of the joint.
Drill Point Geometry and Material Performance
The design of a drill bit – its form and structure such as angles and extensions like wings – plays a role in how the drill screw works with various materials. The ability to grasp these nuances is key in selecting the drill screw for a particular task.
Metal Applications
In metalwork scenarios, a sharp and sturdy drill bit is required to pierce through the material without bending or snapping.
Factors Affecting Performance
Tip Geometry: The shape of the drill bit tip plays a role in how it drills and removes chips from the material being drilled into. A sharper tip angle usually means drilling. May also raise the chances of the bit breaking when drilling into thicker or tougher metals.
Tread Design: The way the threading is designed also affects how well the drills crew works in metal materials; a coarser thread pitch with threads per inch gives grip but needs more force to install; on the other hand finer thread pitch provides weaker grip but is easier to drive in and less likely to damage the surface.
Optimizing for Metal
To enhance the effectiveness of your drills-crews when used on metal surfaces, take into account the following suggestions:
Match the tip geometry to the metal’s thickness and hardness. For thinner gauges, a sharper tip angle can be used. For thicker or harder metals, a more gradual angle is preferred to prevent breakage.
Choose a thread pitch that balances holding power with ease of installation. For thicker metals, a coarser pitch is generally suitable, while a finer pitch might be more appropriate for thinner gauges.
Use lubrication: Applying a lubricant, like cutting oil, to the drill point helps reduce friction, heat buildup, and wear, improving drilling efficiency and extending the life of the drill point.
Control the drilling speed and force: Using a variable speed drill/driver allows you to adjust the RPM (rotations per minute) and the amount of force you apply. This is particularly important for harder metals, where slower speeds and consistent pressure are crucial for preventing overheating and breakage.
Wood Applications
Woodworking screws typically have tips to account for the thickness of the material and include wings to avoid causing the wood to split.
Factors Affecting Performance
Point Length: When choosing drill crews for woodwork purposes, the length of the point plays a role. If the point is too short it could lead to the threads catching before the pilot hole is sufficiently deep resulting in binding and a higher likelihood of breakage. On the other hand, if the point is too long it might stick out through the back of the material posing a safety risk or spoiling the appearance.
Point Wings: Small wings are positioned above the drilling point. Serve as reamers in widening the top part of the hole while driving in the screw to allow the shank to pass through smoothly without catching onto the wood fibers and causing jacking issues—especially handy for thicker wood or when fastening wood to metal by providing space for the screw threads within the wood layer.
Optimizing for Wood
To achieve the outcomes when working with wood applications remember these pointers:
Choose the correct point length: Select a drill screw with a point length that is long enough to drill a pilot hole through the entire thickness of the wood without the threads engaging prematurely.
Consider using wings: When fastening thicker wood or attaching wood to metal, drill screws with wings help prevent jacking and provide a more secure hold.
Control the driving depth: Using a drill/driver with an adjustable clutch allows you to limit the driving torque, preventing the screw from being driven too deep and damaging the material or the screw head.
Qewit: A Reliable Drill Screws Supplier
If you’re looking for top-notch drill screws you can count on them. A wide selection of fasteners with a focus on customer happiness and satisfaction.
Diverse Range and Quality Assurance
With an array of products, in its inventory exceeding 30K variations of fasteners and fixatives for purposes and materials available at Qewit disposal; you can effortlessly locate the suitable drill screws for your specific project needs – be it metalwork or woodworking and other material types alike! The commitment to excellence is evident in Qewit accreditation with ISO 9001 certification – a benchmark for ensuring top-notch quality management practices. Their quality control processes are strong and thorough. They conduct supplier audits. Have in-house testing facilities to guarantee the consistency and trustworthiness of their products.
Conclusion: Choosing the Right Drill Screw for the Job
Choosing the right drill bit is essential for any fastening project because it can greatly influence performance across materials and prevent issues to ensure top-notch outcomes in your workmanship! By following the advice provided in this guide and teaming up with a supplier such as Qewit you can feel assured about your drill bit choices. Create durable connections for all your endeavors.