caTEGORIES
Tags
Self-Tapping Screw Mastery: 5 Rules for Flawless, Long-Lasting Installations
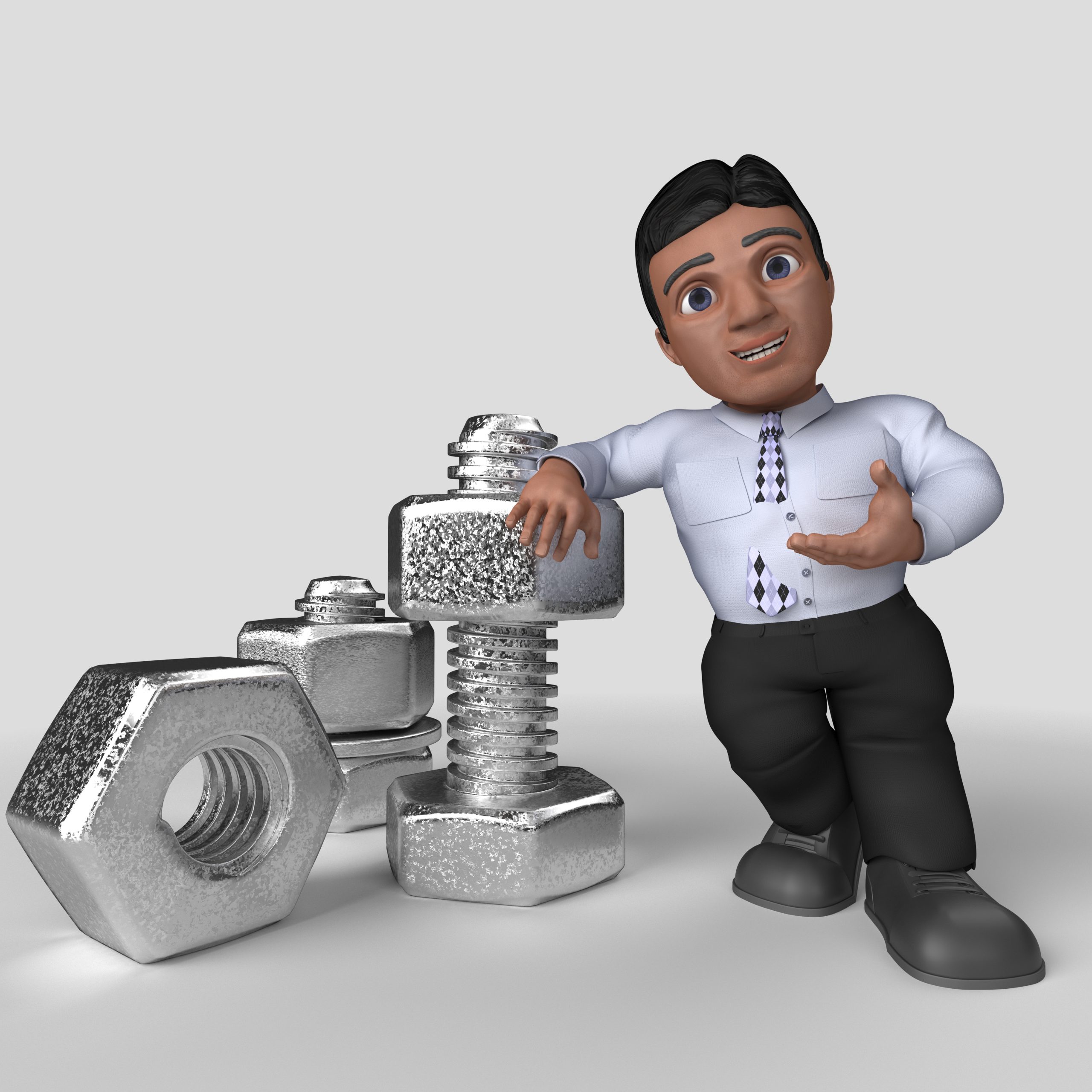
Posted: April 01, 2025
Categories: News
Tags: news
Proper usage of self-tapping screws is the key to perfect and durable installations. The critical part of their use is knowing which kind of self-tapping screw is suitable for your application. They can be installed with adhesive or nails, which is easy and works well.
What Are Self-Tapping Screws?
A multi-functional component of fastening, self-tapping screws are nothing short of ubiquitous. One of the traits that lead them to be the best choice for the application is their ability to generate threads while being inserted into materials. These screws do not require tap holes, so installation is easy and labor time is less. Find out what are its features, types, and what materials are suitable for it.
Key Features of Self-Tapping Screws
Self-tapping screws have special characteristics that differentiate them from standard fasteners. With a sharp or cutting tip, they can pierce through and create their mating threads in their media. This will create a strong grip and will reduce the risk of coming off soon. These screws can also have different kinds of head styles like pan or hexagonal or flat heads depending on the application.
The material they are made from is another important characteristic of them, which are usually using high-grade carbon steel or stainless steel to provide durable construction and a high degree of corrosion resistance. For example, Pan Head Recessed Machine Screws DIN 7985 can be found in durable finishes, including bright zinc plating for excellent corrosion resistance.
Materials Compatible with Self-Tapping Screws
The adaptability of self-tapping screws extends to the range of materials they can work with:
Wood: Commonly used in carpentry for furniture assembly.
Plastic: Suitable for lightweight fixtures.
Metal: Often employed in construction and manufacturing.
For example, products like Hexagon Head Set Screws DIN 933 offer compatibility with diverse materials due to their robust design and corrosion-resistant finishes.
Selecting the Right Screw for Your Project
Choosing the appropriate screw is paramount to ensuring a secure installation, factors such as material type, environmental conditions, and intended application must be considered.
Factors to Consider When Choosing a Screw
Material Type and Thickness
Your choice of screw largely depends on the material you are working with. For example, softer materials such as wood may need thread-forming screws, whereas harder metals need thread-cutting or self-drilling screws. But thickness is also a crucial component; thinner materials might require more shallow screws so they won’t break through. It can be a big consideration for thickness with thinner materials you may need to be screwless to avoid damaging the material.
Environmental Conditions and Corrosion Resistance
Environmental exposure can affect the longevity of your installation. In humid or coastal areas, corrosion-resistant finishes like zinc plating or stainless steel are essential. Products like those offered by QEWIT ensure enhanced performance under challenging conditions.
Recommendations for Specific Applications Using QEWIT Products
For fastening needs in construction projects involving concrete or masonry, consider using concrete screws from QEWIT’s extensive range. These screws deliver exceptional holding power while resisting environmental wear.
Preparing the Installation Surface
Preparation of the surface allows for the best opportunity for the screw threads and the material to make contact with one another, and this is where the real connection is being made. Even minor make-ready grooves or the presence of dust can weaken your fastening system. Removing debris or rust from surfaces to allow for smooth penetration of screws. Self-tapping screws at QEWIT are corresponding to surface-tailored self-tapping screws. Their strong tips and sturdy coatings guarantee consistent functionality even on rough or original surfaces.
Ensuring Torque Installation Security
Using the right torque is key to getting a strong hold without injuring the material or the screw. Torque is the amount of rotational force used when installing. Too low of a torque level can lead to a loose assembly, and too high can pull threads or break the screw. The QEWIT provides clients with technical support and a testing platform to deliver better performance of the products.
Aligning and Positioning the Screw Correctly
Proper alignment of the screws is important to ensure you make a proper fitting that will last a long time and hold. You can experience everything from diminished structural integrity due to misalignment to stripped threads, or even damage to the material. To be exact, always mark your entries on the materials you are using. This is important because it provides a path for the screw to follow when being installed into the luminal wall, preventing misalignment during the procedure.
Another one of the main practices is using the right tools. You can get tools like pilot hole drills or jigs that will help you keep everything straight. Having pilot holes can be useful for harder materials such as metal because they will help overcome the resistance and prevent any splitting or cracking of the substrate. For harder substrates such as metal, pilot holes are critical because they minimize resistance and thus the risk of splitting or breaking the substrate.
QEWIT’s self-tapping screw features a sharp point as well as a cutting-edge screw designed to enable easy penetration into the materials in line. They have very sharp tips, which means they divert very little when inserted, making them a great option for precision applications.
Regular Maintenance and Inspection of Installed Screws
Regular maintenance extends the lifespan of your installations by identifying potential issues early. Over time, factors such as environmental exposure or mechanical stress can weaken screws, leading to failures. Periodic inspections help detect signs of corrosion, loosening, or wear.
If the pendant light is going to be outside or in a wet area, it needs to be examined for rust or corrosion. Screws with corrosion-resistant finishes may help avert these problems. For instance, the brightly zinc-plated Metric Hexagon Full Nuts DIN 934, provides improved corrosion resistance.
QEWIT’s high-quality fasteners are built to last and require minimal maintenance. High-grade materials used in them enable it to function over a long time in tough conditions. While protection is ensured against environmental exposure, features such as anti-corrosion coatings help keep maintenance checks at bay often.
In addition, technical support by QEWIT shall involve testing centers that enable you to evaluate the status of mounted screws accurately. These include tensile strength tests, plating thickness tests (ASTM B-488), and much more to ensure the quality of your installations in the long term. These services range from tensile strength testing to plating thickness testing to help you keep your installations intact for the long haul.
Advanced Tips for Optimizing Self-Tapping Screw Performance
How Can You Combine Screws with Innovative Installation Techniques?
The performance can also be maximized by combining self-tapping screws with advanced installation techniques. For instance, applying the right torque over the tool ensures the correct amount of torque is being used to install the tool.
Another technique involves using lubrication on screw threads when working with dense materials. This reduces friction and makes insertion smoother while minimizing wear on both the screw and substrate.
How Do Advanced Coatings and Materials Enhance Durability?
The service life of the self-tapping screw is directly dependent on the choice of the coating or material. To provide even greater resistance to corrosion, cooking coatings such as zinc flake or hot-dipped galvanization or access to wear resistance are utilized. Such finishes prove to be especially useful for outdoor applications in which contact with moisture is difficult to avoid. Heavy-duty but high-grade materials such as stainless steel, offer extra strength whilst withstanding functionality and wear at different weighing loads. These materials also retain thread integrity over repeated applications.
By leveraging these features alongside innovative techniques, you can significantly improve both the performance and lifespan of your installations.
FAQs
Q1: What tools help in achieving accurate screw alignment?
A: Tools like pilot hole drills and alignment jigs assist in maintaining precision during installation.
Q2: How often should I inspect installed screws?
A: For most applications, regular inspections every six months are recommended; more frequent checks may be needed in harsh environments.
Q3: What coatings provide maximum corrosion resistance?
A: Coatings such as zinc flake or hot-dipped galvanization offer excellent protection against rust and environmental wear.