caTEGORIES
Tags
Material Compatibility with Thread-Forming and Thread-Cutting Self Tappers
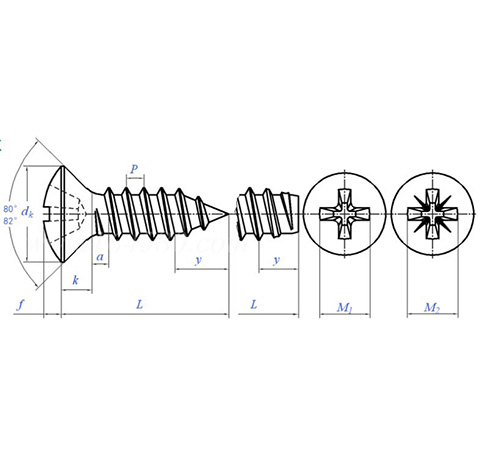
Posted: April 08, 2025
Categories: News
Tags: news
Applying thread-forming and thread-cutting self-tapping screws in the material is necessary to require and verify its compatibility through the characteristics and specifications of the material. Thread-forming screws are typically used in softer materials such as plastic, aluminum, and other soft metals and form threads rather than cutting them.
Overview of Self-Tapping Screws
Self-tapping screws are versatile fasteners used in many industries. Essentially, their distinct design allows them to form their threads while they are being driven into the material, and so have become an important component in many applications. The two broad classes of these screws are thread-forming and thread-cutting design.
How Do Thread-Forming and Thread-Cutting Self-Tappers Differ?
Unlike traditional screws, which remove material, a self-tapping screw only displaces the material to provide the threads. These are suited to situations with softer materials where we need to preserve the integrity. On the contrary, thread cutting self-tapping screws cut material to make threads and so, they are more suitable for tougher substances like steel or hardwood.
What Are the Key Applications of Self-Tapping Screws in Various Industries?
Self-tapping screws are used in construction, automotive, electronics, and appliance assembly. In the world of construction, they need them to fasten metal frames and panels quickly. Automotive industries use them for assembling components with precision and durability.
A self-tapping screw is used for delicate fastening of parts and is required for electronics manufacturers. This is especially suitable for fastening fragile components, as electronics manufacturers often use self-tappers since they can fasten without breaking them.
Factors to Consider When Choosing Between Thread-Forming and Thread-Cutting Self-Tappers
Selecting the appropriate self-tapper involves evaluating several factors to ensure optimal performance and longevity.
How Do Material Properties Impact Screw Selection?
Thread-forming or thread-cutting — material properties will be an important point of consideration. For softer materials, such as plastics, thread-forming screws work best because they minimize stress and cracking. On the contrary, if you are working with harder materials such as steel, you will need a thread-cutting screw that can cut through without any deformation.
What Are the Strength Requirements for Fastening Applications?
The rigidity of the weld is an important factor. This cutting action helps the screw form exactly matching threads in dense materials, often giving them a higher holding power than a comparable threaded portion. Thread-forming screws are better suited to applications where mid-strength clamping is needed and where the design places minimal stress on the substrate.
How Do Environmental Conditions Affect Screw Performance?
Environmental conditions like humidity, temperature changes, or contact with corrosive materials may affect screw functionality. Stainless steel self-tappers or coated self-tappers resist corrosion when used in hostile environments. For example, with a product such as Flat Round Washers DIN 125A, you can provide added protection against corrosion as a result of the galvanized finish.
Compatibility of Thread-Forming Self-Tappers with Different Materials
Understanding material compatibility ensures effective fastening without compromising structural integrity.
Which Materials Are Suitable for Thread-Forming Screws?
Thread-forming self-tappers excel in softer materials such as aluminum, plastic composites, and certain light alloys. Their ability to displace rather than cut through material makes them ideal for these substrates.
Why Choose QEWIT’s Thread-Forming Products for Specific Applications?
A good supplier provides you with quality-related products that you require through a partnership. QEWIT manufactures varied fasteners, like custom thread-forming solutions, that suit several industrial applications. With an undying commitment to quality control and consumer areas of interest, they deliver goods that comply with world-class requirements.
Compatibility of Thread-Cutting Self-Tappers with Different Materials
What Are Common Materials Suitable for Thread-Cutting Screws?
Thread-cutting screws carve out threads by eliminating material and best penetrate harder substrates. They are particularly effective in steel, hardwoods, and dense composites as they penetrate without distorting the surrounding material. Thread-cutting screws make a snug fit in dense metals or hardwoods and help prevent cracking or splitting.
What Are the Advantages of Using QEWIT’s Thread-Cutting Products for Specific Applications?
When you work with a credible supplier, you will have access to high-quality thread-cutting screws for different industrial applications. QEWIT was opened in 2004 and it provides a wide selection of fasteners. They offer custom-tailored solutions based on the unique application needs in a diverse range of industries.
An example is their Hexagon Head Set Screws DIN 933 that is suitable to lock components in high-tensile locations thanks to its heavy-duty design and resistance to corrosion through finishes like zinc plating or hot-dipped galvanizing (HDG). This offers a firm fit and long-lasting performance even in harsh conditions. This guarantees strong fitment but also durable performance in aggressive environments.
Comparing Performance Metrics Between QEWIT’s Thread-Forming and Thread-Cutting Solutions
How Do Torque-to-Tension Ratios Vary Across Different Materials?
There is an important performance metric that the torque-tension ratio when choosing self tapping screws. This is because thread-forming screws require much less torque since they displace rather than cut material. This is what makes them more usable on softer materials like plastics or aluminium alloys. This makes them great for more flexible materials such as plastics or aluminum alloys.
On the other hand, the thread-cutting screws require a larger torque for insertion because it has a cutting action, and present a better tensile strength in more resistant materials. This difference is vital in applications where there is load-bearing capacity like in construction or aerospace.
How Do Durability and Reusability Compare in High-Stress Environments?
When comparing thread-forming and thread-cutting solutions, durability is also a major consideration. A thread-looking screw are often favored in high-stress environments as they produce accurate threads that help keeping hold over time. They are designed to be more durable due to lower wear on the substrate, allowing for repeated usage.
Technically, you can reuse some thread-cutting screws without a loss of performance, but after multiple uses those threads created in the material may eventually degrade. This trade-off is important to consider for all critical applications that require frequent disassembly.
How Does Cost Efficiency Differ in Large-Scale Applications?
Cost-effectiveness is particularly important for factory production lines. Indeed, high volume manufacturing can lower the cost of thread-forming screws when joining softer materials, but thread-cutting screws tend to be more expensive due to the increased complexity of their design and are often only considered if the performance and durability benefits outweigh the cost.
Recommendations for Selecting the Right QEWIT Self-Tapper Based on Material Compatibility
What Guidelines Should Engineers Follow for Material-Specific Projects?
Important to know the characteristics of the material and use the request to choose the right self-tapper. For instance, substrate hardness, working environment, and load-bearing capability of the screws are other factors to consider to ensure whether thread-forming or thread-cutting screws are more practical.
How Can You Leverage QEWIT’s Expertise to Optimize Fastening Solutions?
Working with skilled suppliers guarantees easy access to technical support and custom-made solutions designed around the specifics of your project. By offering the highest levels of customer service with solid quality assurance processes, QEWIT stands out.
If you want to know more about QEWIT, please visit its website!
FAQs
Q1. What is the difference between thread-forming and thread-cutting non-tapping screws?
A: Because they do not remove material but displace it, thread-forming screws are better for softer substrates such as plastics or lighter metals. Thread-cutting screws — these types of screws remove material to create threads, which is why they work great with hard materials like steel and hardwoods.
Q2: Are thread-cutting screws reusable?
A: They can be reused, but because the threads are reformed in the material, it may weaken with multiple uses, depending on the application.
Q3: What certifications are available for fasteners?
A: Certifications such as ISO9001 Quality Assurance and 3.1 certification to DIN-EN-10204 ensure compliance with international standards and product reliability.