caTEGORIES
Tags
Machine Screws vs. Socket Screws: Which Is More Durable?
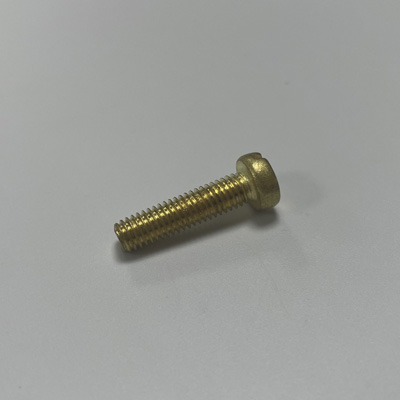
Posted: August 26, 2024
Categories: News
Machine screws and socket screws are essential fasteners that play a pivotal role in various applications. Understanding the differences and applications of these two types of screws is crucial for engineers and manufacturers who need to select the right fastener for their projects. While both screws serve the primary function of joining materials together, each has unique properties that make it suitable for specific situations. This article will delve into the key differences between machine screws and socket screws, exploring their materials, design, strength, applications, and practical considerations.
What Are the Key Differences Between Machine Screws and Socket Screws?
Materials and Manufacturing Process
Machine screws are typically made from a variety of materials, including stainless steel, brass, and carbon steel. These screws undergo a manufacturing process that may include forging, machining, or cold heading, allowing for diverse applications. The versatility in material selection enables machine screws to be tailored for strength and corrosion resistance as per project requirements.
On the other hand, socket screws, also known as socket cap screws, are generally manufactured from high-strength materials such as alloy steel or stainless steel. The manufacturing of socket screws often utilizes processes like cold heading or machining, which provides them with superior strength attributes. The materials used in socket screws often lead to a higher tensile strength, making them suitable for high-stress environments.
Design and Structural Components
Machine screws typically feature a uniform diameter along their entire length with a flat or pan head. The head of the machine screw is designed for use with a standard screwdriver, and its design allows for easy installation and removal. The threads extend the entire length of the screw or partially, which makes them versatile for various fastening needs.
In contrast, socket screws feature a cylindrical head with a hexagonal recessed drive configuration. This design allows for effective torque application and minimizes the risk of stripping the head during installation. Socket screws often have deeper threads that can enhance grip and holding power when installed in a threaded hole or with a nut. This structural design contributes to their overall strength and durability.
Common Applications
Machine screws are widely used in a range of applications, from assembling lightweight fixtures to securing panels and machinery components. Their ease of use and availability in various sizes make them popular in the automotive, electronics, and construction industries. You will find machine screws being employed in situations where quick assembly and disassembly are necessary.
Socket screws, due to their strength and ability to resist shearing, are commonly found in more demanding applications. Industries such as aerospace, automotive, and manufacturing rely on socket screws for securing critical components that experience high levels of stress. They are often used in applications requiring secure fastening without the risk of slippage. In areas where space is a concern, socket screws are advantageous due to their efficient use of height.
How Does Each Screw Type Handle Stress and Strain?
Clamping Pressure and Load Capacity
When considering clamping pressure, both machine screws and socket screws perform effectively, but their capacities differ based on materials and design. Machine screws can handle moderate loads efficiently since they distribute clamping pressure evenly across the surface they fasten. However, their ability to withstand heavy loads may be limited compared to socket screws, especially in high-stress applications.
Socket screws are engineered for greater load capacity and clamping force. Their deeper threads and high-strength materials allow them to maintain grip under significant shear forces. This means that socket screws will likely withstand greater clamping pressures in applications where structural integrity is crucial. Therefore, if your project requires high clamping capacity and durability against fatigue and stress, socket screws could be the better choice.
Resistance to Shearing Forces
Shearing forces can lead to structural failures in fastening applications. Machine screws, while capable, may eventually succumb to these forces if not sized correctly or used inappropriately. For example, in applications subjected to dynamic loads, machine screws might not provide the reliability needed over time.
In contrast, socket screws are specifically designed to resist such shearing forces. Their design and manufacturing process yield a robust fastener that can handle significant stress. As a result, they are favored in applications where components are regularly subjected to high torque, shock, or vibrations, ensuring that the connections remain intact over prolonged use.
What Are the Pros and Cons in Practical Scenarios?
Installation Considerations
When it comes to installation, machine screws generally offer an advantage. Their straightforward installation with a flat or star-shaped screwdriver allows for rapid use in numerous applications. Being highly accessible, you can find machine screw variations available in most hardware stores and online. This can lead to significant time and cost savings on projects requiring frequent installations.
However, socket screws can present a more challenging installation process. Because they require a specific tool — an Allen wrench or hex key — some may find them less convenient to install in some situations. The initial investment in specialized tools may deter some users, but the enhanced strength and durability of socket screws often compensate for the added installation effort.
Maintenance and Replacement Factors
Maintenance is an essential aspect of any assembly. Machine screws may require periodic inspection and tightening, especially in applications exposed to vibration or dynamic loads. Due to their design, there’s also a chance of the heads becoming stripped over time, leading to additional replacement needs.
Socket screws, due to their superior design and robustness, typically require less maintenance once installed. Their resistance to stripping and ability to withstand considerable stress make them a reliable option for long-term applications. While they may sometimes demand more intricate removal processes, their longevity often leads to a lower total replacement cost over time.
In conclusion, both machine screws and socket screws serve unique roles in fastening applications, each with its distinct strengths and weaknesses. By considering the materials, design features, and specific applications, you can determine which type of screw will deliver the durability and performance you require for your projects. Ultimately, the right choice depends on your specific needs and the conditions in which the fasteners will be used.
Which Environments Favor Each Type of Screw?
Exposure to Environmental Elements
When determining the best screw for your project, consider the environmental conditions where it will be used. Machine screws are relatively versatile, but their performance diminishes in harsh environments. For example, if your application is outdoors or in a moisture-rich setting, the type of material used for the machine screws is crucial. Stainless steel machine screws can resist rust, while those made from carbon steel may experience corrosion, which compromises their integrity over time.
Socket screws, crafted from high-strength alloy materials, have superior performance in these environments. Their design often mitigates the risks associated with exposure to environmental elements. When coated with protective finishes, such as zinc or black oxide, socket screws could offer enhanced corrosion resistance, making them ideal for outdoor uses or in moist conditions. Ultimately, evaluating the exposure to environmental elements will help guide you toward the appropriate fastener choice.
Vibration and Movement Tolerance
Understanding how your assembly will be subjected to various movements is equally important. Machine screws may work well in stationary applications; however, they can struggle to maintain their grip under continual vibration. Over time, vibrations can loosen machine screws, requiring regular checks and maintenance to ensure they remain secure. This characteristic can pose challenges in applications like automotive machinery or aerospace components, where consistent vibrations are prevalent.
In contrast, socket screws provide greater resistance to loosening under stress, making them suitable for applications where movement is a factor. Their deeper threads and superior grip enhance their performance under dynamic conditions. When installed properly, socket screws remain secure even in high-vibration environments, thus reducing the risk of failure. In tasks involving vibrations, therefore, opting for socket screws may offer a more reliable outcome.
What Should You Consider When Choosing Between Machine Screws and Socket Screws?
Cost Implications
While both machine screws and socket screws serve essential functions, cost considerations often play a significant role in decision-making. Machine screws typically come at a lower price point due to their widespread availability and simpler manufacturing processes. As a cost-effective option, they are preferable for projects requiring substantial quantities without sacrificing reliability significantly.
On the other hand, socket screws usually command a higher price due to their advanced materials and designs. Although socket screws may require a larger upfront investment, their durability and long lifespan may translate into long-term savings. Therefore, it is prudent to weigh both the initial costs and the potential long-term implications when selecting the appropriate screw type for your specific application.
Compatibility with Existing Systems
Compatibility with existing systems is another critical factor in your selection process. If you’re replacing fasteners in a pre-existing assembly, you may need to consider the thread size, material, and design to ensure cohesion and functionality. Machine screws are widely standardized, making them a generally safe choice for retrofitting projects where matching existing parts is a priority.
However, socket screws may present more compatibility challenges due to their unique head designs. If your assembly already utilizes socket screws, maintaining consistency can enhance performance and minimize unforeseen issues. It’s advisable to evaluate the compatibility of the screws with the materials and components involved in your projects to guarantee successful integration.
Specific Needs of Your Project
Every project has distinctive requirements. When selecting between machine screws and socket screws, assess the unique demands of your application. For lighter assemblies or projects with minimal stress, machine screws may suffice, given their ease of installation and economical benefits. Their adaptability allows usage across a diverse range of industries, making them a practical consideration when custom solutions are not necessary.
Conversely, if your project involves heavy loads, high-stress environments, or safety-critical applications, socket screws emerge as a more robust choice. Their design provides strength under significant torque and helps maintain assembly integrity over time. Being aware of your project’s specific needs can help you make an informed decision about the most appropriate fastener type to utilize.
Stainless Steel Pan Head Machine Screw ISO14583
The stainless steel pan head machine screw, compliant with ISO 14583 standards, is an excellent fastener for general-purpose applications. Its design features a smooth, rounded head, allowing for flush mounting on various surfaces. The stainless steel material offers inherent resistance to corrosion, making this type of machine screw well-suited for indoor and outdoor use.
This type of screw is compatible with numerous threading options, allowing for versatility in applications ranging from electronics to construction. Moreover, the simplicity of installation enhances its appeal in projects where speed and efficiency are vital. When considering machine screws, evaluating the specifics of the stainless steel pan head might be beneficial based on your application requirements.
Stainless Steel Truss Head Machine Screws ASME B 18.6.3
The stainless steel truss head machine screw, adhering to ASME B 18.6.3 standards, provides a broader surface area under the head, distributing the load more evenly. This unique design makes it highly effective for applications needing enhanced grip without the risk of going through the material being fastened. They are predominantly made from stainless steel, ensuring resistance against rust and ensuring durability in outdoor and industrial applications.
These screws also boast a low-profile head which makes them appealing for aesthetics in applications where visibility is a concern. Choosing the right fastener, such as the stainless steel truss head machine screw, could make a notable difference in your project’s overall success, especially when strength and appearance unite in essential applications.
In conclusion, both machine screws and socket screws offer unique characteristics suitable for varying projects. Considering environmental aspects, compatibility, and specific application needs ensures you select the right fastener to meet your requirements effectively. Deliberate on the costs associated, and reflect on the materials and designs that align best with your operational standards before making a choice.