caTEGORIES
Tags
Machine Screw vs. Socket Screws: Expert Insights
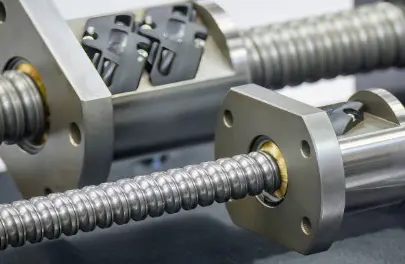
Posted: October 29, 2024
Categories: News
A machine screw is a type of fastener that features a uniform diameter shaft and a head that can be tightened using a screwdriver. These screws are designed for use in machines and similar applications, where they fasten components together with precision. Common applications include automotive parts, machinery assembly, and electronic devices. The versatility of the Phillips Pan Head Machine Screw ASME B18.6.3 provides a reliable solution in various industries due to its compatibility with pre-drilled and tapped holes.
Materials Used in Machine Screws
Machine screws can be crafted from various materials to meet specific application requirements. Typical materials include carbon steel, stainless steel, and brass. The choice of material impacts the strength, durability, and corrosion resistance of the screw. For instance, stainless steel machine screws are favored in environments prone to moisture, as they offer superior resistance to rust and corrosion. When selecting a screw, you should consider the environment it will be used in, ensuring optimal performance and longevity.
How Do Socket Screws Differ from Machine Screws?
Socket screws, often known as set screws, have a cylindrical head and are typically driven through the use of an internal hexagon or other shaped drive. The main difference between socket and machine screws lies in their design and application. Socket screws are frequently employed in situations requiring a compact design or where the screw head must be recessed to prevent interference with another object. This type is prominent in various mechanical equipment and assemblies where space is a premium.
Material Options for Socket Screws
Like machine screws, socket screws are manufactured from numerous materials, including carbon steel and stainless steel. The application and required strength will dictate the choice of material. Carbon steel socket screws might be used in applications where weight-saving is necessary and corrosion resistance is not a concern, while stainless steel options are optimal for environments where humidity and corrosion are prevalent.
Which is More Durable: Machine Screws or Socket Screws?
When discussing durability, both machine screws and socket screws have their strengths based on material choice and intended application. Machine screws like the Phillips Pan Head Machine Screw ASME B18.6.3 exhibit durability due to their broad head design that disperses load, allowing them to resist stripping and fatigue better in high-stress environments. In contrast, socket screws are designed for situations where compactness is required, which may influence their load-bearing capacity under specific conditions.
Clamping Pressure Performance
Clamping pressure performance should be evaluated depending on the intended application. Machine screws typically provide higher clamping force because they are often used in conjunction with nuts and washers, maximizing tension and load capacity. However, socket screws can deliver significant holding power if properly torqued and used in applications that require such design. Therefore, the best choice largely hinges on the specific requirements of your project.
How Do You Choose Between Machine Screws and Socket Screws?
Selecting between machine and socket screws hinges primarily on your project’s specific needs. If your application requires easy access for tightening or loosening, machine screws are often more advantageous. On the other hand, should the design necessitate a recessed head for clearance, socket screws would be the appropriate choice. Consider factors such as potential exposure to vibration, load environments, and overall assembly access to determine the optimal screw type for your needs.
Selecting the Right Bolt Size
Once you’ve chosen the type of screw, determining the correct size is crucial to ensure secure fastening. For instance, when working with the Pan Head Recessed Machine Screws DIN 7985, you need to consider screw diameter and length in relation to the materials being fastened. The right fit will enhance performance and prevent stripping or breakage, which could compromise project integrity. Always verify specifications against your requirements and consult product guidelines to avoid sizing errors.
In conclusion, both machine screws and socket screws serve unique purposes in assembly while offering various options concerning material, design, and application. For further assistance regarding your fastener selections or inquiries regarding products like the Pan Head Recessed Machine Screws DIN 7985, don’t hesitate to contact us. For reliable fasteners and a wide selection, visit Qweit.
Advantages of Using Machine Screws Over Alternative Fasteners
Machine screws offer distinct advantages when compared to wood screws and self-tapping screws. Unlike wood screws, which are designed primarily for use in wood, machine screws come with a more uniform shaft that facilitates efficient fastening in metal and plastic components as well. When you need precision and reliability in tight assemblies, machine screws like the Phillips Pan Head Machine Screw ASME B18.6.3 provide that crucial level of consistency. Additionally, unlike self-tapping screws that create their own threads upon insertion, machine screws can be used in pre-drilled holes, allowing for easier disassembly and reassembly without damaging the fastening surface.
Under specific conditions, machine screws may outperform both wood screws and self-tapping screws in various applications. For instance, machine screws are commonly used in heavy machinery and automotive applications, where strength and durability are paramount. In these scenarios, the reliability of a well-engineered machine screw ensures the components remain securely fastened under heavy loads and vibrations. Furthermore, a properly fitted machine screw can withstand cyclic stresses better than its counterparts.
Specialized Use Cases
Machine screws also excel in specialized applications where unique characteristics or fitment requirements are essential. In electrical applications, machine screws are used for securing components such as circuit boards and enclosures, where precision and ease of assembly are highly valued. The ability to achieve a precise torque on these screws is critical to the reliability of electrical connections.
Another specialized use case can be found in the aerospace and automotive industries, where machine screws must meet stringent industry standards for performance and safety. These applications usually impose precise material and grade specifications, making machine screws the preferred choice. You may also find machine screws in manufacturing settings where repetitive assembly tasks occur; the uniformity of the screw design facilitates quick and efficient assembly by machine or human operator alike.
Advantages and Disadvantages of Socket Screws
Socket screws are known for their high torque capabilities, which provide significant benefits in heavy-duty applications. The internal drive design allows for better grip when utilizing a wrench or socket, enabling you to apply higher torque without risking cam-out, a common issue with traditional Phillips heads. This feature makes socket screws particularly suitable for high-stress environments where significant clamping force is required.
When installed correctly, socket screws can hold components tightly together, minimizing play and enhancing assembly integrity. However, it’s essential to ensure that you’re using the right tools and techniques, as overtightening can lead to damaging the screw or the surrounding material. A well-implemented torque specification guideline will help ensure you maximize the benefits of socket screws while avoiding potential drawbacks.
Sleek Design Benefits
One of the hallmark features of socket screws is their sleek design, which fits seamlessly into tight spaces. The recessed head allows for easy access in confined areas, simplifying the fastening process in applications where traditional screw heads may be intrusive. This compact design is beneficial in machinery or equipment where space is a factor, contributing to overall efficiency in assembly and maintenance procedures.
Moreover, this design feature contributes to a cleaner aesthetic, as the socket screw is less likely to protrude from the surface of the assembly, reducing the chances of snagging or catching on clothing or tools. A recessed head can also protect the screw from potential damage, offering enhanced longevity and reliability in use. You will appreciate the balance between functionality and design when you incorporate socket screws into your projects.
Material Considerations in Choosing Fasteners
Choosing the right material for machine screws and socket screws is vital in determining their overall performance and suitability for your application. While both types of screws are available in materials such as carbon steel, stainless steel, and brass, each offers its own set of advantages. For instance, stainless steel screws are known for their superior corrosion resistance, making them ideal for use in environments exposed to moisture, chemicals, or high humidity.
On the other hand, carbon steel screws may be more cost-effective and provide superior tensile strength in dry environments. This factor makes them suitable for applications that require high strength at a lower cost. However, they are more susceptible to rust and corrosion compared to their stainless steel counterparts. By evaluating the material strengths and weaknesses, you can make informed decisions that align with the conditions and requirements of your project.
Explore more fastening solutions at Qweit
When considering materials, it’s also critical to account for the specific grades available within each type. For example, machine screws may be categorized into various grades like 4.8, 8.8, etc., each indicating different tensile strengths and mechanical properties. The grade you select can have a profound impact on the performance of the screw in specific applications, especially when subjected to varying loads and conditions.
In some applications, composite materials are gaining traction. These materials tend to balance lightweight properties with adequate strength and corrosion resistance. As the fastener industry continues to evolve, being aware of emerging materials and their unique benefits could provide a competitive edge, allowing for enhanced performance while reducing costs.
In conclusion, both machine screws and socket screws serve distinct roles in various applications. By considering factors such as the advantages of machine screws, the capabilities of socket screws, and essential material considerations, you can improve the quality and efficiency of your projects. For further assistance regarding your fastener selections or inquiries regarding products like the Pan Head Recessed Machine Screws DIN 7985, don’t hesitate to contact us. For reliable fasteners and a wide selection, visit Qweit.