caTEGORIES
Tags
How to Install a Flange Nut Properly for Maximum Durability
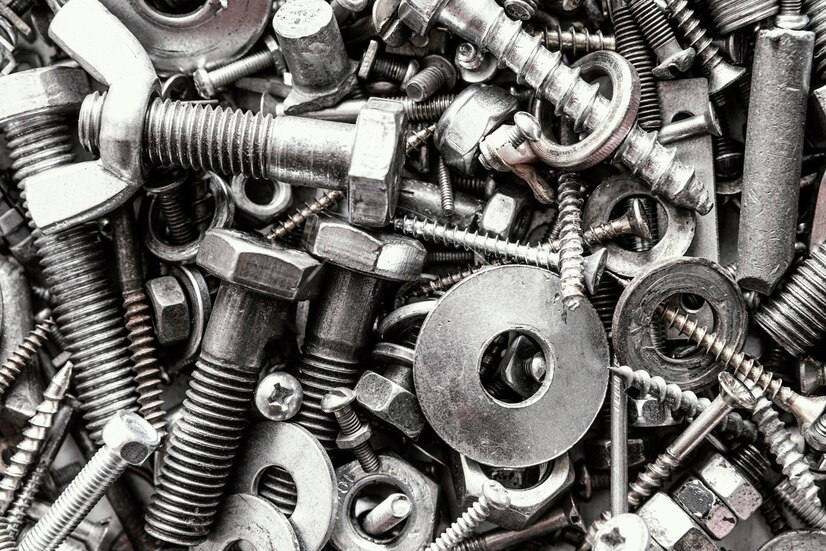
Posted: November 07, 2024
Categories: News
Flange nuts are an integral part of many mechanical assemblages and play a vital fastening role. These nuts are commonly wide-flanged which provides a large surface area that helps to spread the load and reduce potential damage of the connected components. Incorporating a flange nut in your assembly can provide greater durability and functionality, delivering more powerful, lasting joints.
Understanding Flange Nuts and Their Importance
What is a Flange Nut?
A flange nut is a nut that has an attached washer, the flange being part of the nut itself. It also makes it so that the flange nut sits flush line with the surface of the workpiece thus stopping any pull-through as well.] Flange nuts have a distinctive body, which is extremely effective against loosening as a result of vibration and this trait makes them ideal for confection in mechanical applications that face fluctuating forces.
Key Applications of Flange Nuts
Flange nuts are used in many fields such as automotive, aerospace, and construction. They are widely used in assemblies for which stability and strength become the prime requirement. In such applications, flange nuts hold components including engines, suspensions, and even wheels together in automobiles while withstanding severe operating conditions.
Benefits of Using Flange Nuts in Mechanical Assemblies
There are many advantages of adopting this type of fastener in your making. The design ensures effective weight distribution thus minimizing the chances of damaging connected components. Also, they hold strong against resisting looseness caused by vibration which contributes to the stability of your assembly and enhances performance and service life. In addition, it can be convenient with flange nuts that they come in a wide range of shapes and sizes but also materials and surfaces to make the perfect combination for your project.
Tools and Materials Needed for Installation
To accurately train for a flange nut, appropriate installation is vital along with the appropriate tooling and materials. With the right gear with you in the first place, you can noticeably enhance your output and stay clear of several typical blunders that include incompatible arrangements. Making certain that you have a good supply of the right tools, can help you deliver better quality in your work and avoid the common downfalls that may come with bad installation.
Essential Tools for Installing a Flange Nut
Tools Required to Properly Install a Flange Nut Essentially, the primary tools are the socket wrench/right angle it specifically gives you leverage to make sure you tighten off both nuts. An adjustable wrench helps in getting into tight spaces, if necessary. Finally, you will also want to have a torque wrench available so that you can accurately apply the necessary amount of force when installing your new components without risking damaging anything from over-tightening.
Recommended Materials for Ensuring Durability
Selecting the proper pieces to complement your installation is just as important. Using quality flange nuts in materials like stainless or high-grade alloys, for example, can significantly improve the durability of your assembly. In addition, use fasteners like bolts and washers that work with the flange nut design to further promote a secure and durable joint. When sourcing your materials, consider Qewit as they have many products. Specializes in the manufacture of superior quality flange nuts suitable to meet heavy-duty industrial specifications for your projects.
Step-by-Step Guide to Installing a Flange Nut
Successfully installing a flange nut requires careful attention to detail and a structured approach. By following these simplified steps, you can achieve a precise installation that promotes durability and reliability.
Preparing the Assembly Area
The assembly area should be clean and organized before installation. Clean up all the debris and stuff that will hinder the installation process. A tidy workspace not only keeps you focused but also minimizes the risk of injury during assembly. Also, check that the components to be used for joining do not contain dirt or impurities as they can negatively impact the flange nut fitting.
Aligning the Bolt with the Flange Nut
After preparing your workspace, make sure that the bolt lines up exactly with the flange nut. Importantly, the bolt threads must not have any dirt or thread damage caused by another installation that might prevent proper bolt fit and/or affect the reliability of the joint. Screw the flange nut onto the bolt by hand and make sure it sits on top of the surface. Be sure to avoid cross-threading as this will cause stripping, and be less effective at fastening.
Tightening Methods for Maximum Durability
Hand Tightening Techniques
Next, thread the flange nut onto the bolt and secure it by hand-tightening methods. First thread the nut clockwise until it is tight against the assembly. At this point, it should be tightened just enough that all of the pieces stay together and are unable to shake loose using minimal force. This means that it fits well enough for a quick hand tightening and lessens the chances of over-torquing.
Utilizing Torque Wrenches
Then, once it is hand-tightened, a torque wrench should be used for maximum durability. Torque wrenches provide precise control over the amount of force applied, preventing damage from overtightening. Check the specs for the specific flange nut and bolt being utilized; they will tell you what the torque settings should be. Tighten the flange nut to the specified torque using the even force applied again on the assembly.
Verifying Proper Installation and Adjustment
Once you have installed it, you must check the correctness of your work. This step requires you to examine the space so that everything is in place and tight, and check if your flange nut sits properly. Rework if required and verify that the assembly is within specification. By regularly inspecting and taking care of your assembly, you can help promote longevity and function for the flange nut to continue doing an outstanding job!
With this invaluable guide and quite high-grade flange nuts, you can rest assured of a stable mechanical assembly that lasts. With this extensive guide and high-quality flange nuts, you are guaranteed a strong, reliable, and long-lasting mechanical assembly.
Common Mistakes to Avoid During Installation
Over-tightening or Under-tightening Concerns
One of the most common mistakes during the installation of a flange nut is miscalculating the amount of torque applied. Over-tightening can lead to stripping of the threads or even deforming the nut itself, thereby reducing its effectiveness. Conversely, under-tightening can result in excessively loose fittings, making it susceptible to vibrations that can ultimately lead to failure in the connection. It’s crucial to utilize a torque wrench and follow the recommended specifications meticulously to avoid these pitfalls.
Ignoring Compatibility between Materials
Another key concern in the installation process is the failure to ensure compatibility between the flange nut, bolt, and the materials being joined. When different materials are used, varying coefficients of thermal expansion could cause loosening over time due to temperature fluctuations. Additionally, using materials that do not bond well can lead to corrosion or other forms of degradation, compromising the integrity of the assembly. Be sure to choose flange nuts that are made from a suitable material that matches the application requirements, such as those offered by Qewit, which specializes in high-quality, compatible products.
Neglecting Periodic Maintenance Checks
Lastly, neglecting periodic maintenance checks is a mistake that can lead to premature failure of your assembly. Regular inspections allow you to detect any signs of wear and tear, such as rust or loosening of the flange nut, before they escalate into more significant issues. Establish a routine to check the condition of the flange nut and surrounding components, and perform necessary adjustments or replacements to enhance the longevity and reliability of your assembly.
Selecting High-Quality Products from quit
Introduction to Qewit’s Line of Flange Nuts
When it comes to selecting flange nuts, quality is paramount, and Qewit sets the standard for excellence in this field. Their line of flange nuts is engineered to meet stringent performance criteria, providing superior load distribution and resistance to loosening. Each flange nut is subjected to rigorous testing to ensure its consistency and durability in a variety of applications, from automotive to industrial uses. By choosing Qewit, you gain access to exceptional products designed to withstand the demands of any assembly, granting you peace of mind for every application.
Where to Purchase Qewit Flange Nuts
Qewit offers a complete range of flange nuts that are conveniently accessible from their easy-to-navigate website as well as through authorized distributors, in various locations. If you need help with choosing the right nut for your application, detailed specifications and informative resource details to assist in selection are available on the website. Local distributors can provide an informed decision for the in-person statures people not only have to check out but simply clichés. By choosing quit flange nuts, you are securing components that emphasize durability and performance for your projects — ensuring that all of your installations are carried out to the best possible specifications.
By avoiding common installation mistakes and selecting high-quality flange nuts from Qewit, you can create robust, durable connections that meet both user requirements and performance expectations.