caTEGORIES
Tags
How Self Tapper Material Influences Performance in Varied Environments
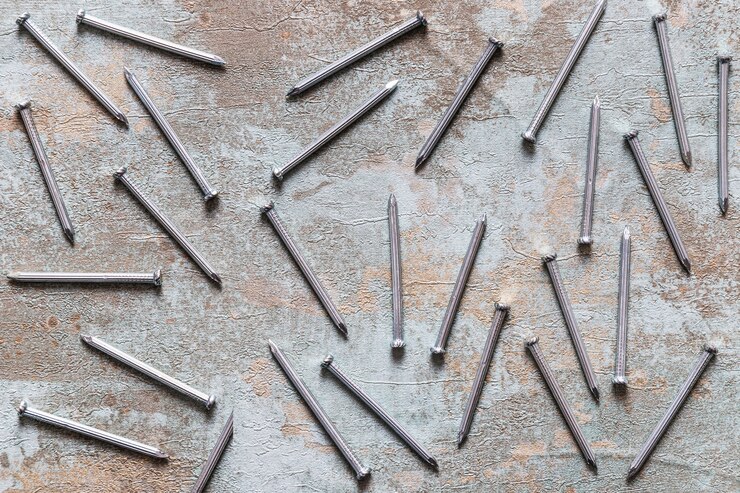
Posted: September 05, 2024
Categories: News
The type of material used in a self-tapping screw is crucial, for how it works in situations. With fastening needs growing in fields picking the material is more important than ever. Knowing how different materials affect self-tappers is key for experts aiming to improve their fastening methods, in conditions. This piece delves into why material choice matters the usual materials chosen, what influences these choices, and the environmental obstacles that can affect performance.
Importance of Material Selection for Self-Tappers
Choosing the materials is crucial, for self-tapping screws to work well as it affects how strong, durable, and resistant they are, to conditions. Picking the material can guarantee that it lasts long and performs reliably, especially when faced with situations. Moreover, the material used also influences how easy it is to install them and ensures a fastening without any stripping or breaking. With industries requiring uses it becomes essential to choose materials that are best suited for specific environments.
Common Materials Used in Manufacturing Self-Tappers
Hardened Steel
Hardened steel is frequently used in self-tapping screws because of its resistance, tension, and lasting nature. These screws can endure loads. Are commonly used in demanding tasks. Nonetheless, hardened steel can corrode, which makes it less suitable for humid settings unless protected with a coating. Despite the drawbacks the benefits of utilizing hardened steel in controlled environments surpass them making it a preferred option, for securing structures.
Stainless Steel
Stainless steel is highly valued for its ability to resist corrosion making it a great option, for use in places where there’s a lot of moisture or corrosive materials. The increased flexibility of steel self-tapping screws also results in performance when dealing with sideways pressure. Even though they may not be as tough, as hardened steel screws stainless steel screws offer a way to secure materials without sacrificing looks in architectural endeavors.
Titanium
Titanium screws are gaining popularity, in industries that need lightweight materials like aerospace and medical sectors. Titanium is known for its resistance to corrosion making it ideal for conditions, like saltwater exposure and high humidity. Despite being pricier their lightness and strength boost efficiency making them a premium choice mainly used for tasks.
Factors Influencing the Choice of Material
Several factors come into play when deciding on the appropriate material for self-tapper manufacturing. The application context, including load requirements, and potential exposure to chemicals or environmental stressors, plays a significant role. Additionally, the cost of materials can be a deciding aspect, particularly for larger projects where the budget is a constraint. Customization options and coatings are also considered to enhance the performance traits of certain materials, further aiding in making a well-informed decision.
Environmental Challenges and Their Impact on Self-Tappers
Corrosive Environments
Self-tappers are often utilized in environments exposing them to corrosive agents, which can lead to premature failure if unsuitable materials are chosen. For instance, in marine applications, the presence of saltwater can induce rapid corrosion in steel materials, while stainless steel and titanium would excel in such scenarios. Understanding how different materials react under varying corrosive conditions allows engineers to make pertinent choices that enhance performance and safety.
Effects on Different Materials
The efficacy of different self-tapper materials under corrosive environments can vary quite considerably. Regular carbon steel may quickly succumb to damage, while stainless steel’s chromium content provides a layer of protection against rust. In these environments, considering surface treatments and coatings alongside material choice becomes evermore pertinent to mitigate the risks of failure due to corrosion.
High-Temperature Environments
Self-tappers operating at elevated temperatures require materials that can resist thermal expansion and maintain integrity. Hardened steel tends to lose its effectiveness at high temperatures as it may become brittle, while stainless steel and titanium showcase more resilience in these settings. The conductivity of materials also plays a role in environments that experience thermal extremes, impacting performance outcomes.
Material Resilience and Conductivity
Resilience is crucial when selecting materials for high-temperature applications. Stainless steel continues to perform effectively, maintaining its structural strength despite exposure to heat. Although titanium can also endure high temperatures, its excellent strength-to-weight ratio makes it particularly advantageous when weight reduction is a priority. Each material’s thermal conductivity must also be assessed, as it affects heat dissipation and, by extension, the longevity of the fastening solution.
Moisture and Humidity Considerations
Moisture and humidity pose significant challenges to the integrity of self-tapping screws, potentially leading to corrosion and degradation. Selecting non-corrosive materials is essential to ensure long-lasting performance in environments subject to water exposure. Furthermore, recognizing that even protective coatings can wear down over time under humid conditions helps in understanding maintenance and replacement intervals for fastening systems.
Optimizing Design for Different Environments
Adjusting Manufacturing Techniques Based on Material
The manufacturing techniques of self-tapping screws must align with the specific material chosen to ensure optimal performance. For instance, the processes used to craft hardened steel self-tappers may vary significantly when producing stainless steel or titanium options. Factors such as thermal treatments for hardness enhancement or machining methods for precision cutting become crucial in utilizing each material’s properties effectively. Additionally, the production techniques can influence the surface finish, which directly impacts the self-tapper’s ability to penetrate materials and create a secure connection.
Manufacturers should also consider the influence of environmental conditions on the production process. For example, in regions with high humidity, manufacturing facilities should maintain stringent controls to prevent materials from absorbing moisture during production, thereby compromising the quality of the self-tappers. Furthermore, advancements in technology, including automated equipment for precise manufacturing, can help ensure consistent quality across varying materials. Overall, adapting manufacturing techniques to the nature of the self-tapper materials leads to improved performance in targeted applications.
Enhancing Coatings and Treatments for Environmental Resistance
Coatings and treatments applied to self-tapping screws serve as a vital line of defense against corrosive and extreme environmental influences. Selecting the right type of coating, such as zinc plating or polyamide, can significantly enhance the self-tapper’s resistance to oxidation and wear. These coatings create a barrier that prevents moisture and chemicals from penetrating the material’s surface, thus extending the screw’s lifespan. In addition, surface treatments like passivation for stainless steel can improve corrosion resistance by promoting a more uniform oxide layer.
In high-temperature settings, specialized coatings might be necessary to maintain structural integrity while providing oxidation resistance. Thermal barrier coatings are an example that helps self-tapper materials withstand extreme heat conditions without degrading. Moreover, understanding the compatibility of coatings with different materials is essential, ensuring that the applied layer does not adversely affect the self-tapper’s performance. Enhanced coatings and treatments ultimately contribute to a more durable and reliable fastening solution that performs consistently across varied environments.
Performance Evaluation of Self-Tappers by Material Type
Durability and Longevity in Varied Conditions
The durability of self-tapping screws largely depends on the material composition and the environmental conditions in which they are utilized. For instance, hardened steel self-tappers, while robust and reliable in dry and controlled environments, may exhibit reduced longevity in moist or corrosive situations unless properly coated. On the other hand, stainless steel screws are well-regarded for their ability to withstand adverse conditions, making them suitable for outdoor applications where exposure to humidity and pollutants is a concern. Titanium self-tappers, due to their inherent resistance to corrosion and wear, tend to outperform both hardened and stainless steel in extreme environments, ensuring consistent performance over prolonged periods.
Moreover, the installation process can also influence durability. Self-tappers that are installed correctly not only provide strong connections but also help in prolonging the overall system life. Professionals must be aware that improper installation can lead to failures, thus negating the advantages of high-quality materials. Considering these factors helps in selecting the right self-tapper for enhanced durability and longevity in varied conditions.
Load-Bearing Capacity Across Different Materials
Load-bearing capacity is a critical aspect of self-tapper performance, as it directly correlates with the material’s properties. Hardened steel, known for its high tensile strength, can support substantial loads, making it a common choice for structural applications. However, in scenarios where precise load distribution is essential, stainless steel offers a superior alternative due to its ductility and flexibility, allowing for performance that withstands dynamic forces without compromising integrity. The choice of material, therefore, must take into account the specific load requirements of the application, ensuring that the selected self-tapper will effectively support the intended weight without risk of failure.
Titanium screws are a choice when you need to lighten the load without compromising strength. The impressive strength-to-weight ratio of titanium makes it ideal for supporting loads in aerospace applications where excessive weight can impact operational efficiency. Engineers must carefully assess load requirements and material properties to make the choice, for real-world performance.
Resistance to Wear and Tear
In conditions, it’s crucial, for self-tapping screws to withstand wear and tear. The performance of these fasteners can be greatly impacted by friction, abrasion, and impact. Although toughened steel screws are sturdy they may gradually wear out in high friction scenarios, necessitating checks and replacements. On the hand, self-tapping screws crafted from steel or titanium are less likely to wear out easily offering extended durability in challenging environments. Their resistance to rust also contributes to their longevity since even slight surface deterioration can result in declines, in performance.
Moreover, surface treatments and coatings are crucial, for enhancing wear resistance. Methods like galvanizing or using polymer coatings can add a coating thereby prolonging the lifespan of self-tapping screws in challenging conditions. By comprehending the wear properties of materials experts can choose the self-tapping screws, for settings leading to enhanced system reliability and decreased maintenance requirements.
As industries progress the need, for quality self-tapping screws, such as the ones provided by Qewit is on the rise. The materials and designs they offer play a role in delivering reliable fastening solutions that excel in different settings. With Qewits’ dedication to excellence and creativity, customers can have confidence that their ventures will benefit from notch self-tapping screws tailored for longevity, strength, and durability, against wear and tear.