caTEGORIES
Tags
How Do Cap Head Bolts Improve Efficiency in Automated Manufacturing?
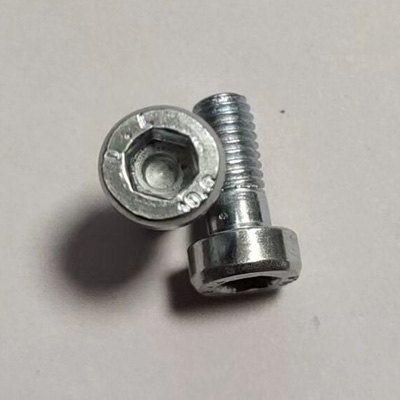
Posted: November 05, 2024
Categories: News
Cap head bolts are significant in automated manufacturing since they allow the manufacturers to improve their efficiency. Cap head bolts are great fasteners and enhance mechanical stability; they ease production by simplifying the required fastening components. Designed with high-reliability characteristics, such bolts provide precise functioning of machinery that ultimately leads to increased productivity in assembly lines.
Understanding the Role of Cap Head Bolts
Types and Features of Cap Head Bolts
Cap head bolts come in various types, each designed to meet specific manufacturing needs. They can be classified based on their dimensions, material composition, and intended application.
Material Specifications
They are typically manufactured from carbon steel, stainless steel, or brass, ensuring they can withstand varying environmental conditions.
Dimensional Standards
Cap head bolts conform to particular dimensional standards like DIN, ISO, etc. Sizes available M3-60, Lengths of 6mm to 400 mm That standardization makes sure that cap head bolts slip right into current manufacturing processes. Standardization of cap head bolts enables them to integrate smoothly into current manufacturing systems.
The Functionality of Cap Head Bolts in Machinery
Cap head bolts contribute significantly to the functionality of machinery. They provide the necessary stability and reliability required for consistent performance in automated manufacturing applications.
Torque Control and Stability
The design of cap head bolts allows for enhanced torque control during installation, minimizing the risk of over-tightening or loosening. This stability is essential, as fluctuating torque can lead to mechanical failures over time.
Load Distribution
Head cap bolts are designed to spread the load evenly across joint surfaces. By distributing the load uniformly, this design minimizes stress concentrations which can be important in high-stress applications where automated manufacturing is required. The even distribution of load leads to a reduction in stress concentrations and is advantageous in high-stress applications such as those in automated manufacturing.
Impact on Manufacturing Assembly Lines
Cap head bolts have a profound impact on the efficiency of manufacturing assembly lines. Their design features not only simplify assembly processes but also enhance overall mechanical performance.
Simplifying Assembly Processes
Using cap head bolts simplifies assembly processes, allowing workers to focus on precision rather than compatibility issues.
Precision Alignment Advantages
Cap head screws allow for the exact setup of parts This guarantees every single piece is tailored perfectly, which minimizes off-setting that eventually causes wastage or faults in the product. This will ensure that each part is precisely indexed so there are fewer chances of misalignment which can create waste or defective product.
Reduction in Assembly Time
The incorporation of cap head bolts leads to a substantial reduction in assembly time. The ease of insertion and secure fastening contribute to quicker assembly cycles, maximizing productivity.
Enhancing Mechanical Performance
The mechanical performance of machines can be significantly enhanced by using quality cap head bolts, which are designed to endure demanding conditions.
Durability Under High-Stress Conditions
During heavy-duty applications, cap head bolts are ideal due to their high-stress conditions. You can rest assured that even during heavy use, they will not compromise because of their high level of tensile strength. They have a high tensile strength, providing peace of mind that they will NOT be bending or cracking under heavy use.
Importance in High-Speed Operations
Cap head bolts are critical for high-speed operations, such as those found in automated manufacturing environments. Withstand rapid motion and vibrations, ensuring the general stability of mechanical systems, and enabling uninterrupted production flows. They are resistant to fast movements and vibrations and maintain stability within the complete production system turning into a non-stop float of production.
Qewit manufactures quality Cap head bolts according to standard DIN912 and also the product according to standard ISO4762 They offer cap head bolts in many styles including carbon steel, stainless steel, and manufacturing options to fit your business ambitions. Every bolt has been exquisitely built — durable and tough enough to withstand the harshest conditions. Whether for features such as zinc plating or features that need high corrosion resistance, Qewit solutions are designed to meet your production specifications. Introducing Qewit cap head bolts could be the very upgrade that your manufacturing process is searching for to reach peak efficiency and reliability.
Qewit has a huge emphasis on standards Qewit cap head bolts can be provided in different grades/sizes for form lightweight construction material design until heavy industrial use. Going to Qewit products translates into quality and efficiency, which can permeate through your manufacturing line. Moving to Qewit products means power and quickness, a form that carries efficiently over to your assembly line.
By choosing Qewit, you are not just opting for fasteners but investing in a reliable partner for your manufacturing needs.
Explore the following facts and find out how cap head bolts can play a vital role in improving operational efficiency in automated manufacturing environments. The capabilities for optimal torque control, load distribution, and mechanical performance with higher levels of integration help in faster assembly while reducing the risk associated with operation. These advantages can be optimized even more by adopting Qewit products which makes it a good decision for manufacturers looking to enhance productivity and quality of the product.
Recommendations for Implementing Cap Head Bolts by Qewit
Selection Criteria Based on Application Needs
However, the following selection criteria particular to an application should be examined when evaluating Qewit’s cap head bolts. While choosing a gear motor for system design, a few aspects like the working environment, load requirement, and interoperability with other elements used must be evaluated carefully. Choosing stainless steel cap head bolts offers durability and resistance against corrosion for applications that are shipped with corrosive elements. In heavy machinery applications, for example, 10.9 or even 12.9 bolts are required – the tensile strength of these high-grade steels provides reliability under extreme loads.
In addition, consideration has to be given to what dimensional standards are needed. With Qewit’s cap head bolt, it follows international standards like DIN and ISO so the needed features as a standard can be easily attached to existing systems.
Qewit acknowledges that each manufacturing environment is unique with different requirements, and provides tailored solutions for respective applications. From a size perspective, you can choose from cap head bolts offered in their extensive catalog that provides customization availability on the aspect of material type as well as surface finish. This versatility ensures that manufacturers can discover the perfect bolt for every unique requirement, ultimately increasing efficiency.
Support and Services Provided
In addition to its product offerings, Qewit takes pride in offering a wealth of support and service with which the cap head bolts can be integrated into any manufacturing operation. The service involves technical consultancies to analyze and recommend suitable products for the relevant applications. On top of that, Qewit also assists during the design & engineering phase in optimizing the component usage.
And, they back their purchase-ready package with customer service that not only supports users as the system is set up during the installation process but also through troubleshooting to measure the machine or tool’s performance after setting it up. The holistic approach substantiates the reliability of their products and fosters long-lasting relationships with clients aiming for operational excellence. This comprehensive method strengthens their products as trusted entities and fosters long-term relationships with clients who focus on optimum operational prowess.
Integration Techniques for Optimized Results
Efficient integration of cap head bolts into manufacturing processes is key to realizing their full potential benefits. Applying best practices and proven integration methods will maximize performance and efficiency, ensuring that production lines operate smoothly.
Best Practices for Installation
Accomplishing proper installation of cap head bolts is critical for achieving optimized results in manufacturing operations. Utilizing a calibrated torque wrench is recommended to ensure accurate torque specifications are met, preventing over-tightening that may cause assembly failures.
Moreover, ensuring that mating surfaces are clean and free from debris will facilitate better torque distribution and enhance the reliability of the joint. Proper alignment of all components during assembly will prevent any undue stress on the bolts, contributing to a longer service life. Lastly, regular inspections post-installation can help identify any potential issues before they escalate, ensuring consistency in manufacturing efficiency.
Proven Integration Methods
Implementing cap head bolts in manufacturing lines can be streamlined through several proven integration methods. First, structured assembly line protocols should be established that dictate the order of operations and assign specific tasks related to bolt installation. This organized approach minimizes downtime and boosts overall productivity by reducing errors that can slow operations.
Training operators on the nuances of handling and installing cap head bolts can further enhance integration effectiveness. Offering workshops or instructional materials ensures that workers understand the importance of proper installation techniques and the impact of quality fasteners on operational efficiency.
Lastly, incorporating regular maintenance schedules aimed at inspecting and tightening cap head bolts contributes to creating a robust manufacturing environment that prioritizes efficiency and reliability. Using these integration techniques not only promotes operational excellence but also ensures the longevity of production machinery and components.