caTEGORIES
Tags
Fastener Certifications 101 Navigating Industry Standards
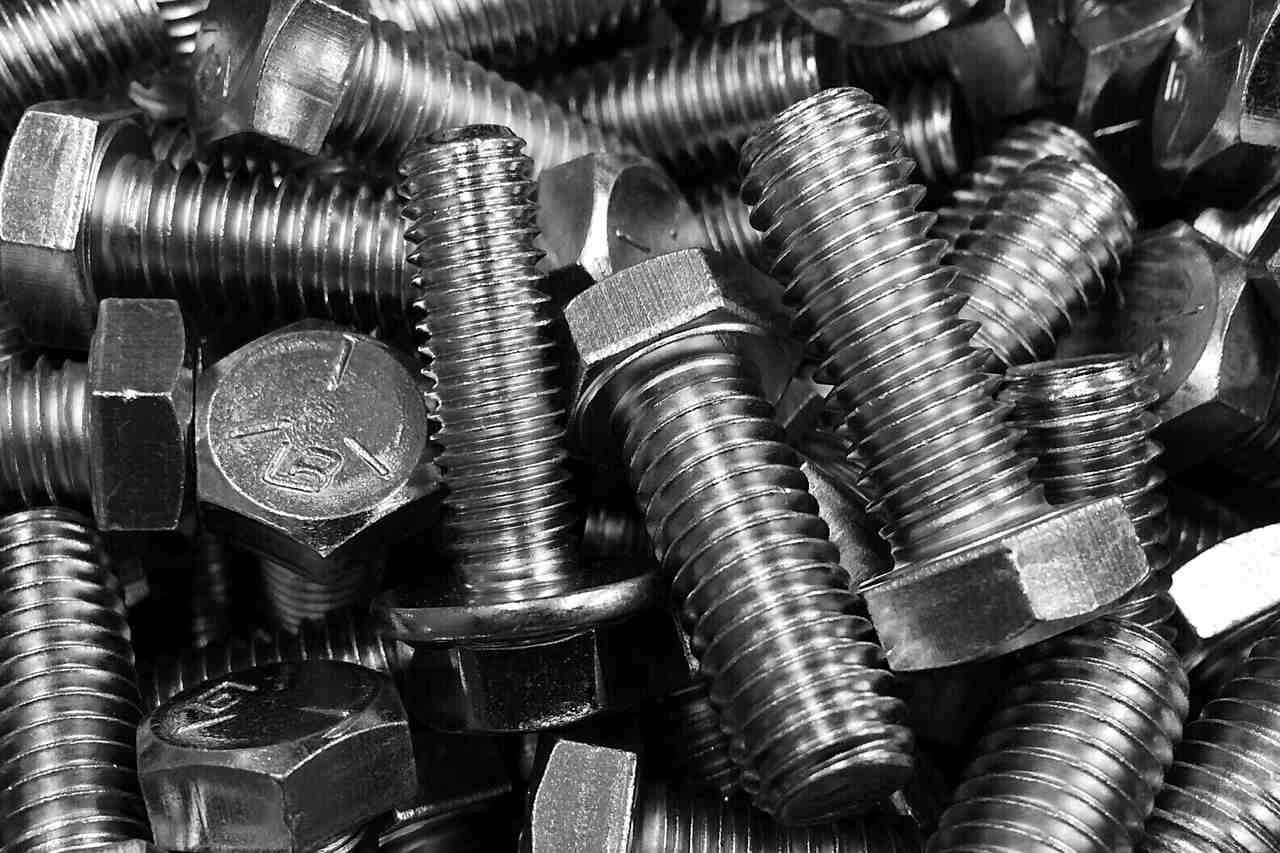
Posted: July 11, 2024
Categories: News
Tags: news
In the current dynamic manufacturing environment, comprehending the certifications and industry standards relevant to fasteners is essential. These benchmarks guarantee and utilized the quality of fasteners from aerospace to construction. For producers and vendors, adhering to these stringent criteria is not merely a matter of compliance but also a means of offering reliability assurance to their clientele.
Understanding Fastener Certifications
Importance of Certifications in the Fastener Industry
Certifications play a critical role in guaranteeing that fasteners meet predefined standards for performance, quality, and safety. These certifications aim to see people from across the industries can find fasteners that fits their requirements. this can lower the possibility of dysfunctions and withstand their intended applications. this is vital for the efficiency and safety of every operation.
Common Types of Fastener Certifications
Common fastener certifications include ISO (International Organization for Standardization), ASTM (American Society for Testing and Materials), and SAE (Society of Automotive Engineers) standards. Different industries may require adherence to different certifications based on their unique safety and performance needs. These certifications typically cover mechanical properties, material composition, and manufacturing processes.
How Certifications Impact Quality and Safety
Certifications impact the quality and safety of fasteners by enforcing stringent testing and documentation protocols. This ensures that each fastener complies with specific requirements that entail durability, strength, and corrosion resistance. Certified fasteners provide confidence to engineers and manufacturers, knowing that they can rely on these components for critical and high-stress applications.
Key Industry Standards for Fasteners
Overview of International Standards
International standards act as crucial benchmarks for the design, manufacturing, and testing of fasteners, ensuring uniformity and reliability across global markets. By complying with these standards, manufacturers can guarantee the compatibility and interoperability of fasteners in a variety of international applications.
ISO Standards
ISO standards are globally recognized and cover various aspects related to the performance, dimensions, and manufacturing of fasteners. These standards are often updated to reflect new technology and methodologies.
ASTM Standards
ASTM standards focus on materials and their properties, influencing the selection process for fasteners in industries like construction, automotive, and aerospace. They specify requirements for chemical composition, mechanical properties, and testing methodologies.
DIN Standards
Originating from Germany, DIN standards set forth stringent guidelines for fastener specifications. These standards are commonly adopted across Europe and emphasize precision and reliability.
Regional Certification Bodies and Their Regulations
Regional certification organizations develop particular standards that address the unique demands of local industries and adhere to regional regulatory mandates.
North American Bodies (SAE, ANSI)
In North America, SAE and ANSI play a vital role in standardizing fasteners. These bodies set performance and safety guidelines that are crucial for automotive and engineering applications.
European Regulations (EN, CE Marking)
European standards such as EN and CE marking ensure that fasteners are compliant with EU regulations. These certifications often overlap with ISO and DIN standards, reinforcing the importance of consistency and reliability.
Asian Standards (JIS, GB)
Standards like JIS (Japanese Industrial Standards) and GB (Guobiao standards from China) regulate the manufacture and use of fasteners in Asia, ensuring they meet regional requirements and applications.
Obtaining Fastener Certifications
Steps to Certification for Manufacturers
Manufacturers aiming for certification must follow several procedural steps, which include submitting an application, adhering to established guidelines, and conducting comprehensive tests on their products. This process guarantees that each certified fastener complies with the essential industry standards.
Documentation and Testing Requirements
Proper documentation and exhaustive testing are required to achieve certification. This includes detailed reports on material properties, manufacturing processes, and performance evaluations to ensure compliance.
Role of Third-Party Certification Bodies
Third-party certification bodies provide unbiased assessments of fasteners to verify compliance. Their impartial evaluations add an additional layer of credibility to the certification process and reassure customers about the quality and safety of the products.
Benefits of Certified Fasteners for Businesses
Increased Market Acceptance
Certified fasteners are more readily accepted in global markets because they adhere to recognized standards. This enhances their marketability and widens the customer base.
Assurance of Quality and Performance
Certifications provide assurance of quality and performance, instilling confidence in businesses regarding the reliability of their fasteners. This assurance is crucial in high-stakes scenarios where failure is unacceptable.
Compliance with Regulatory Requirements
Adhering to industry standards and securing relevant certifications ensures compliance with regulatory requirements. This helps businesses avoid legal issues and potential penalties related to non-compliance.
Challenges in Maintaining Compliance with Standards
Keeping Up with Changing Standards
Industry standards and certifications frequently evolve to accommodate new technologies and practices. Keeping up-to-date with these changes is essential but can be challenging for manufacturers.
Costs Associated with Certification Processes
Achieving and maintaining certifications can be costly due to the extensive testing, documentation, and regulatory compliance required. These costs can be a significant burden for smaller manufacturers.
Addressing Non-Compliance Issues
Failing to comply can result in significant consequences such as product recalls and legal sanctions. It is crucial to address these matters swiftly and efficiently to uphold reputations and ensure operational effectiveness.
Future Trends in Fastener Certifications
Advances in Testing and Verification Technologies
The future of fastener certifications will likely see advances in testing and verification technologies. These improvements will enable more precise and efficient certification processes.
Movement Towards Global Harmonization of Standards
There is an ongoing movement towards the global harmonization of industry standards, which would simplify certification processes and ensure consistency in fastener quality worldwide.
Impact of Sustainability and Environmental Criteria on Certifications
Sustainability and environmental criteria are becoming increasingly important in the evaluation of fasteners. Future certifications will likely place greater emphasis on eco-friendly materials and manufacturing processes.
Qewit
Since its establishment in April 2004, Qewit has distinguished itself as a benchmark for quality and reliability in the industrial fasteners industry. Qewit has gained the trust of many as a supplier of industrial consumable products, particularly fasteners, sourced from mainland China and nearby regions such as Taiwan, Malaysia, Vietnam, and Thailand. The company’s British ownership has played a crucial role in this achievement by implementing strong Supply Chain Management practices that guarantee high quality and operational efficiency.
Qewit’s advantageous positioning and extensive network enable it to provide a diverse array of fasteners tailored to meet the specific needs of various industries. The company’s steadfast dedication to quality is evident in its stringent sourcing protocols, which adhere to international standards. This commitment to excellence is especially critical when dealing with the complexities of fastener certifications and industry standards.
Compliance with industry standards is vital for guaranteeing the reliability and safety of fasteners in a multitude of applications. Qewit excels in this domain, offering products that not only meet but frequently surpass the necessary certifications. Whether it’s ISO, ASTM, or other pertinent standards, Qewit’s fasteners are engineered to meet the most rigorous requirements, providing clients with confidence and assurance.