caTEGORIES
Tags
Essential Tips to Inspect and Maintain Fasteners for Optimal Performance
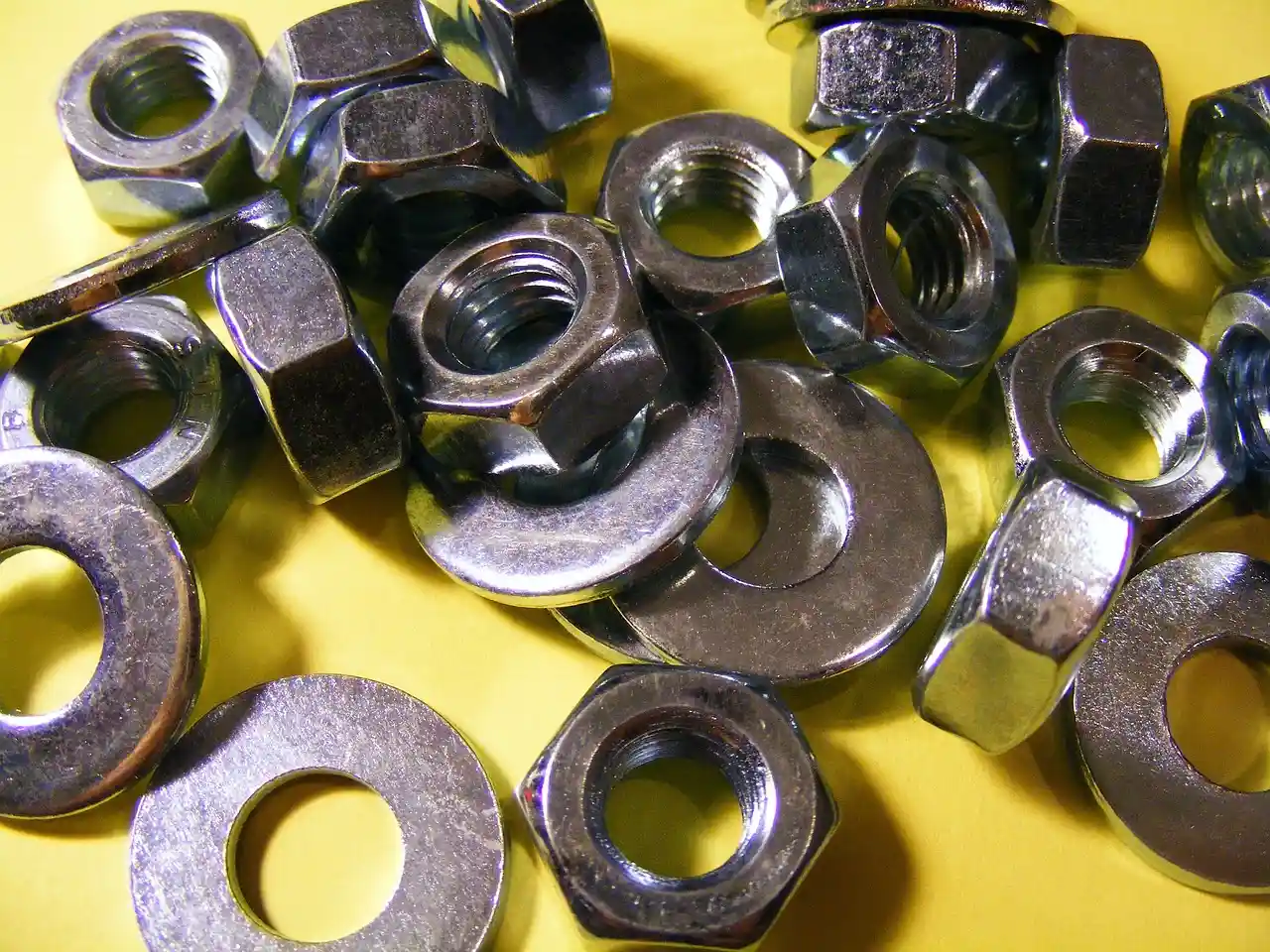
Posted: July 25, 2024
Categories: News
Tags: news
Understanding the Importance of Fastener Inspection and Maintenance
Fasteners are crucial for maintaining the structural integrity of any construction, machinery, or assembly. These small yet vital components ensure that all parts stay securely connected, thereby enhancing the overall safety and functionality of the structure. Without proper inspection and maintenance, even the most dependable fasteners can become compromised, potentially leading to system failures and expensive repairs.
Neglecting the maintenance of fasteners can result in significant risks. The lack of attention can lead to the development of rust and corrosion, weakening the fastener’s hold over time. Additionally, fasteners may suffer from regular wear and tear, ultimately undermining the strength and safety of the connected parts. Regular inspection and routine care are paramount to avoid operational disruptions and ensure the longevity of the assembly.
Different applications require various types of fasteners, each designed to fulfill specific roles. Common types include bolts, screws, nails, rivets, and washers. Each type of fastener offers unique advantages tailored to particular uses, and understanding their specific maintenance needs is crucial for sustaining optimal performance.
Founded in 2004, Qewitco has persistently focused on producing and trading high-quality, reliable products. The company’s operational principles, which are deeply influenced by its former British owners and directors, have been crucial in managing the supply chain of industrial consumable goods from mainland China and neighboring countries such as Taiwan, Malaysia, Vietnam, and Thailand. This combination of Western business expertise and Far Eastern values enables Qewitco to provide outstanding products and services to its international customers.
Qewitco‘s competitive product range includes fasteners of general grade, high grade, and those made from brass/copper, stainless steel, aluminum, and various alloys. The provision of test certificates, coupled with rigorous professional quality control and traceability, underscores the company’s unwavering commitment to excellence.
Regular Inspection Protocols for Fasteners
Effective fastener maintenance begins with a regular inspection protocol, tailored to identify potential issues before they escalate. Establishing a consistent inspection routine ensures that all fasteners remain in peak condition, safeguarding the integrity of any structure or machinery.
Daily Visual Inspections
Conducting daily visual inspections is a simple yet efficient approach to identifying early signs of wear and tear. By routinely examining fasteners, it becomes easier to detect problems such as noticeable rust, corrosion, or loosening. Daily checks should involve scrutinizing the positioning and condition of all fasteners to confirm they are secure and free from immediate harm.
Weekly Torque Check Procedures
In addition to daily visual inspections, weekly torque checks are vital. Using a torque wrench, verify that each fastener maintains the correct tension as specified by the manufacturer. Inadequate or excessive torque can lead to failures or inefficiencies, compromising the strength of the joins. Maintaining proper torque levels helps in sustaining the fasteners’ effectiveness throughout their lifespan.
Monthly Detailed Inspection Steps
Monthly inspections offer an opportunity to perform more thorough evaluations and proactive maintenance. This process involves several steps to ensure comprehensive assessment and upkeep of fasteners.
Inspect for Rust and Corrosion
Rust and corrosion are common issues that can severely impact a fastener’s performance. Using a magnifying glass, examine the fasteners for any signs of rust or corrosion, which often appear as reddish-brown spots or a flaky texture. If rust is detected, it’s crucial to clean the area and apply rust protection to prevent further degradation.
Check for Wear and Tear
Frequent use can lead to wear and tear on fasteners, impacting their performance. During the monthly check, examine each fastener for indications of abrasion, distortion, or stripping. Fasteners that exhibit significant wear and tear should be replaced right away to prevent compromising the entire structure or system.
Evaluate Thread Condition
The threads of fasteners play an essential role in maintaining a tight grip. Carefully inspect the threads for any signs of stripping or damage that could affect their performance. Damaged threads can lead to loosening over time, reducing the effectiveness of the fastener. If thread damage is observed, the fastener should be replaced to maintain the structural integrity of the assembly.
In conclusion, regularly inspecting and maintaining fasteners is a critical practice for ensuring their ongoing efficiency and the reliability of any connected system. By incorporating daily visuals, weekly torque checks, and monthly detailed inspections into your maintenance schedule, you can safeguard your fasteners against common degradations, prolong their life, and prevent costly failures.
Effective Methods to Maintain Fasteners
Cleaning and Lubrication Techniques
Maintaining the cleanliness and proper lubrication of fasteners is vital for ensuring their longevity and optimal performance. Regular cleaning removes debris and contaminants that can lead to corrosion and other forms of degradation, while proper lubrication minimizes friction and wear, facilitating smoother operation and easier maintenance.
Recommended Cleaning Agents
Selecting the appropriate cleaning agents is essential for effective cleaning. Solvent-based cleaners like mineral spirits and denatured alcohol are ideal for eliminating grease and oil residues. For milder contaminants, a solution of mild detergent and water can be sufficient. It’s vital to steer clear of harsh chemicals that might harm the fastener material. Moreover, employing a soft-bristle brush or cloth can assist in thoroughly cleaning grooves and threads without causing abrasion or damage.
Proper Lubrication Practices
Proper lubrication practices play a crucial role in bolstering the performance and lifespan of fasteners. Begin by selecting the appropriate lubricant, such as anti-seize compounds for high-temperature environments or silicone-based lubricants for general applications. Before applying, ensure the fastener is thoroughly clean and dry, which helps the lubricant adhere better. Apply the lubricant evenly, making sure it penetrates the threads and other critical areas. Regular lubrication checks should be part of your maintenance routine to ensure continuous protection against wear and friction.
Protective Coatings and Treatments
Advanced protective coatings and treatments can significantly enhance the durability of fasteners, especially in harsh environments. These methods provide an extra layer of defense against rust, corrosion, and other forms of degradation, thereby extending the lifespan of the fasteners.
Anti-Corrosion Coatings
Anti-corrosion coatings are an effective way to protect fasteners from environmental damage. These coatings, such as zinc plating, phosphate coatings, and hot-dip galvanizing, create a barrier between the metal and corrosive elements. Applying these coatings during the manufacturing process ensures comprehensive coverage. For ongoing maintenance, inspect the integrity of these coatings regularly and reapply as needed, especially if signs of wear or exposure are evident.
Heat Treatment Processes
Heat treatment processes, such as annealing, tempering, and quenching, play a crucial role in enhancing the strength and durability of fasteners. These treatments modify the material’s microstructure, thereby increasing its resistance to wear, fatigue, and stress. By incorporating heat treatment into the manufacturing process or during maintenance, the performance of fasteners under different load conditions can be optimized. Regularly inspecting for indicators of heat treatment degradation, like discoloration or structural changes, is essential for timely reapplication and maintaining the integrity of the treatment.
Tools and Equipment for Fastener Inspection and Maintenance
Essential Tools for Routine Checks
Incorporating essential tools into your maintenance routine is key to performing effective inspections and ensuring the reliability of fasteners. These tools help identify and correct issues before they lead to failures.
Torque Wrenches
Torque wrenches are indispensable for verifying that fasteners are tightened to the correct specifications. They provide precise control over the torque applied, helping to prevent over-tightening or under-tightening. Using a torque wrench regularly during maintenance checks ensures that all fasteners maintain the appropriate tension, reducing the risk of structural compromise.
Calipers
Calipers are precise measuring instruments used to check the dimensions of fasteners. By measuring the diameter, length, and thickness of fasteners, calipers help ensure they meet the necessary specifications and tolerances. This tool is particularly useful for detecting subtle deviations and wear that could affect performance.
Thread Gauges
Thread gauges play a crucial role in examining the pitch and integrity of fastener threads. They are instrumental in detecting threading problems such as pitch discrepancies, wear, or deformation. By using thread gauges regularly, one can avert thread-related failures by making sure that fasteners remain correctly and securely fitted.
Advanced Diagnostic Equipment
To further enhance the effectiveness of fastener maintenance, advanced diagnostic equipment can be employed. These tools provide detailed insights into the condition of fasteners, uncovering issues that are not visible to the naked eye.
Ultrasonic Testing Devices
Ultrasonic testing devices utilize high-frequency sound waves to detect internal flaws or stress points within fasteners. This non-destructive testing method allows for the identification of cracks, voids, and other hidden defects that could compromise fastener integrity. Regular ultrasonic testing helps in proactively addressing potential failures before they occur.
X-Ray Fluorescence (XRF) Analyzers
X-Ray Fluorescence (XRF) analyzers are advanced tools used to detect the elemental composition of fasteners. This technique provides precise information on material grade and potential contaminations. Regular use of XRF analyzers can ensure that fasteners meet material specifications and are free from harmful impurities, thus maintaining their performance and reliability.
Incorporating a mix of these tools and methods allows for the thorough inspection and upkeep of fasteners, ensuring their operational integrity and prolonging their lifespan. By integrating these procedures into your regular maintenance plan, you can guarantee ongoing performance and avert unexpected breakdowns, which in turn results in safer and more dependable assemblies.
Addressing Common Issues with Fasteners
Identifying Signs of Over-Tightening
Over-tightening is a common issue with fasteners that can lead to various structural problems. Signs of over-tightening include stress marks on the fastener head and distorted threads. These stress marks indicate that excessive force has been applied, which can compromise the integrity of the fastener. Distorted threads may lose their grip, leading to unintended loosening over time. Regular inspections should involve checking for these indicators to promptly address any over-tightening issues and replace compromised fasteners if necessary.
Dealing with Loosening Problems
Loosening of fasteners can occur due to vibrations, thermal expansion, and cyclical loading. When a fastener becomes loose, it can lead to misalignments and potential failures of the connected components. To address this, it is essential to inspect fasteners frequently, especially in high-vibration environments. Applying thread-locking compounds or using lock washers can help mitigate the risk of loosening. Additionally, maintaining appropriate torque levels during installations can prevent initial looseness and ensure a more secure fit.
Replacing Damaged or Worn Fasteners
Damaged or worn fasteners must be replaced promptly to maintain the integrity and safety of the assembly. Inspection should focus on identifying visible damage such as cracks, deep abrasions, or significant corrosion. Any fastener exhibiting these signs should be removed and replaced with a new one that meets the original specifications. Ensuring that the replacement fastener is of the same material and grade is crucial to maintain uniform performance and avoid introducing weaknesses into the structure.
The Importance of Record Keeping in Fastener Maintenance
Documenting Inspection Findings
To effectively maintain fasteners, it is crucial to meticulously document all inspection findings. This includes noting the condition of the fasteners, any problems detected, and the corrective actions taken during inspections. Such thorough documentation results in a detailed maintenance history. This history is invaluable for monitoring fastener performance over time and spotting recurring issues that might need more significant intervention. Furthermore, keeping accurate records supports compliance with regulatory and safety standards, serving as proof of proper maintenance practices.
Tracking Maintenance Activities
Tracking all maintenance activities related to fasteners is crucial for maintaining continuous operational reliability. Detailed logs should note all routine inspections, cleaning, lubrication, and any replacements carried out. By systematically tracking these activities, maintenance teams can ensure that no steps are overlooked and that each fastener remains in optimal condition. This systematic approach not only enhances the longevity of fasteners but also helps in planning future maintenance schedules and in procuring necessary replacement parts in a timely manner.
In conclusion, addressing common issues with fasteners such as over-tightening, loosening, and wear requires regular and thorough inspections. Implementing protective measures, promptly replacing damaged or worn fasteners, and maintaining detailed records of all maintenance activities are essential practices for ensuring the continued performance and reliability of fasteners in any assembly. Adopting these strategies will lead to safer, more efficient operations, minimizing the risk of unexpected failures and costly repairs.
Companies such as Qewitco Fasteners Co., Ltd. play a pivotal role in this process by supplying high-quality fasteners that meet stringent quality control standards. Their commitment to excellence ensures that the fasteners used in industrial applications can uphold the structural and functional demands placed upon them. Combining robust products with precise fastening techniques enables industries to promote both safety and efficiency.