caTEGORIES
Tags
Effective Solutions for Corrosion in Outdoor fasteners
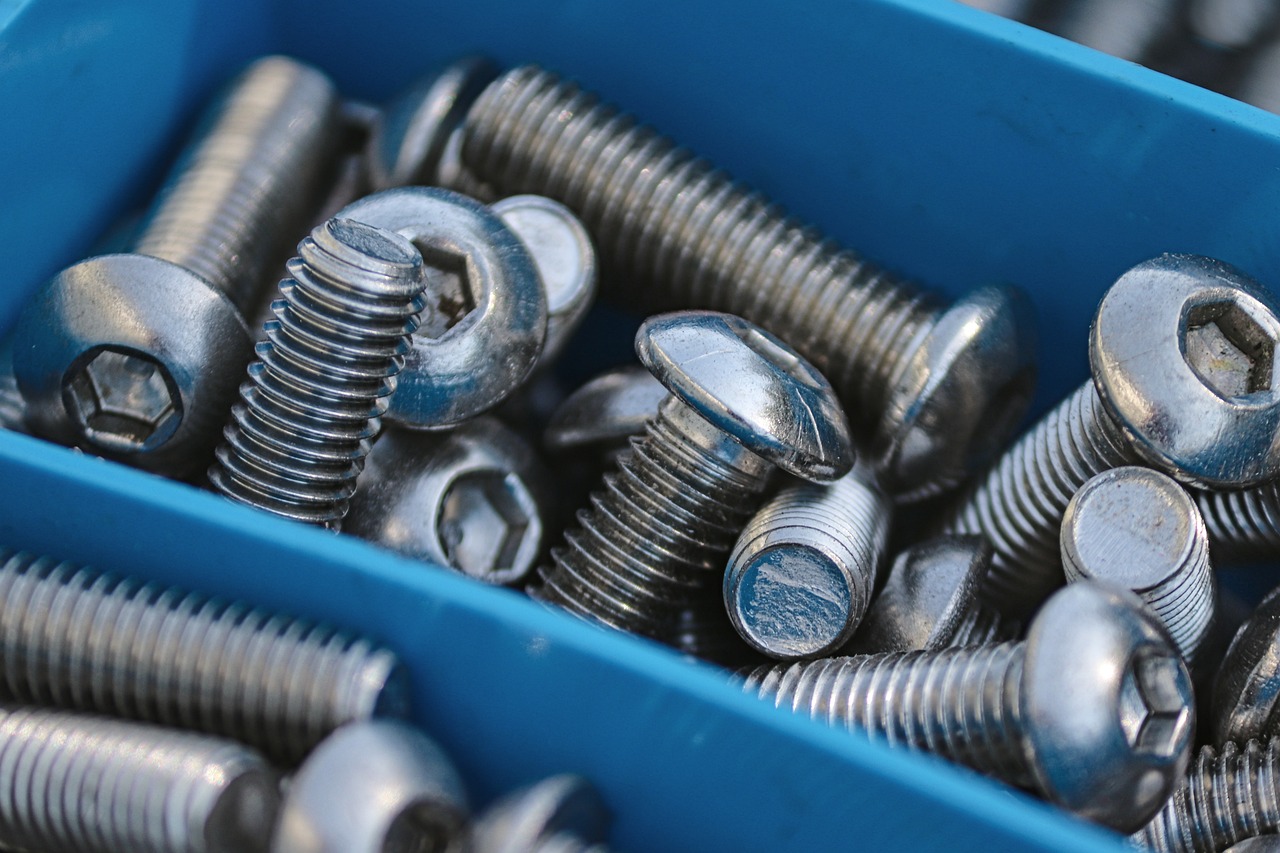
Posted: August 13, 2024
Categories: News
Understanding Corrosion in Outdoor fasteners
Fasteners play a critical role in construction and assembly, particularly in outdoor and marine settings. Corrosion in these fasteners can cause them to weaken and fail, leading to safety hazards and higher maintenance expenses. It’s important to understand the various types, causes, and effects of corrosion on fasteners to choose the right solutions and materials.
Types of Corrosion
There are several types of corrosion that can affect fasteners in outdoor environments. The most common include general or uniform corrosion, which occurs evenly over the surface, and galvanic corrosion, which happens when two dissimilar metals are in contact in the presence of an electrolyte. Pitting corrosion, identified by small, deep pits on the metal surface, is also prevalent in chloride-rich environments like coastal areas. Crevice corrosion, caused by stagnant moisture in confined spaces, can equally be problematic.
Causes and Effects of Corrosion on fasteners
Corrosion on fasteners is usually triggered by exposure to moisture, oxygen, and salts or chemicals. When fasteners corrode, their structural integrity is compromised, leading to potential failures in the applications they are intended to secure. Corroded fasteners lose their mechanical properties, resulting in decreased load-bearing ability and operational inefficiencies. Over time, the cost implications of replacing corroded fasteners and rectifying subsequent damages can be significant.
Common Environments Prone to Corrosion
Fasteners used in various environments face different corrosion challenges. Coastal and marine environments, due to high salt content in the air and water, are highly corrosive. Industrial areas, where pollutants and chemicals are present, also pose risks for fastener corrosion. In addition, outdoor construction sites subject to rain, humidity, and temperature fluctuations offer favorable conditions for the onset of corrosion. Therefore, selecting the right fasteners for specific environments is critical to extending their lifespan.
Material Selection for Corrosion Resistance
Selecting the appropriate material for fasteners is crucial in reducing corrosion. Certain materials are particularly noted for their corrosion resistance and are frequently chosen for outdoor and marine environments.
Stainless Steel fasteners
Stainless steel fasteners are renowned for their excellent corrosion resistance. This is due to the presence of chromium, which forms a passive oxide layer that protects the underlying metal from corrosion. Grades like A2-70 and A4-70 are commonly used because of their balance between strength and resistance to corrosion, particularly in marine environments where they provide reliable performance.
Aluminum and Titanium Alloys
Aluminum and titanium alloys are also favored for their corrosion-resistant properties. Aluminum has a natural oxide layer that safeguards it against corrosion and is lightweight, making it ideal for applications where both properties are valuable. Titanium, although more expensive, offers superior corrosion resistance and high strength, making it suitable for highly corrosive environments.
Coated and Plated fasteners
Coated and plated fasteners provide an additional layer of protection against corrosion. Zinc plating, for example, creates a barrier that prevents moisture and corrosive elements from reaching the underlying metal. Mechanical galvanization and other coating technologies also offer enhanced protection for carbon steel fasteners, ensuring durability in corrosive outdoor conditions.
Protective Coatings and Treatments
Different protective coatings and treatments can be applied to significantly improve the corrosion resistance of fasteners utilized in outdoor environments or marine locations.
Introducing Qewitco, the epitome of excellence in the world of fasteners and fixings. As a formally British wholly owned business, Qewitco has established itself as a reliable supplier of fine quality products to customers across the globe. With a strong focus on producing and trading premium and consistent quality products, Qewitco has become a trusted name in the industry.
Qewitco offers a wide range of fasteners and fixings, catering to various needs and requirements. Their competitive product lineup includes fasteners of general grade, high grade, as well as fasteners made of Brass/Copper, Stainless Steel, aluminum, and alloys. With a commitment to quality, Qewitco provides test certificates and ensures professional quality control and traceability for their products.
What sets Qewitco apart is their dedication to customer satisfaction and their Western-style approach to business. They understand the importance of delivering value for money and offer a worry-free service from production to delivery. With a focus on account management, quality control, and customized special products, Qewitco goes above and beyond to meet customer needs.
Galvanization Process
Hot-Dip Galvanizing
Hot-dip galvanizing involves immersing the fastener in molten zinc, creating a robust and durable coating that provides excellent protection against corrosion. The thickness of the zinc layer ensures long-term resistance to environmental factors, making it ideal for heavy-duty outdoor applications.
Electro-Galvanizing
Electro-galvanizing, on the other hand, applies a thinner layer of zinc through an electrochemical process. While the resulting coating is not as thick as that from hot-dip galvanizing, it still offers significant corrosion resistance and is suitable for less demanding outdoor applications.
Powder Coating
Powder coating involves applying a dry powder to the fastener surface, which is then cured under heat. This treatment provides a durable and aesthetically pleasing finish that resists chipping, scratching, and corrosion. Powder coating is available in various colors and thicknesses, offering both protection and customization for outdoor fasteners.
Anodizing Process for Aluminum fasteners
Anodizing strengthens the natural oxide layer on aluminum fasteners, greatly boosting their resistance to corrosion. This electrochemical procedure not only shields the fastener but also provides the added advantage of producing a decorative finish that can be dyed in a range of colors. Anodized fasteners are exceptionally well-suited for use in environments exposed to severe elements.
Design Considerations to Prevent Corrosion
In addition to material selection and protective treatments, certain design considerations can help prevent corrosion in outdoor fasteners.
Proper Drainage and Avoiding Water Traps
Ensuring that fasteners are used in designs that promote proper drainage can prevent water from accumulating around them. Avoiding water traps, where moisture can stagnate and cause corrosion, is essential. Properly designed joints and fastener placements will facilitate water runoff, mitigating the risk of corrosion.
Minimizing Dissimilar Metal Contact
Galvanic corrosion occurs when two different metals are in contact in a conductive environment. By minimizing the contact between dissimilar metals or using insulating materials such as nylon washers, the risk of galvanic corrosion can be significantly reduced.
Using Isolation Techniques
To prevent corrosion, isolation techniques such as using non-metallic fasteners or applying coatings to avoid direct metal-to-metal contact can be effective. Methods like bonded washers or gaskets serve as barriers against moisture ingress and provide electrical separation between dissimilar metals, thus enhancing the longevity of the fasteners.
In conclusion, addressing corrosion issues for fasteners used in outdoor or marine environments requires a multifaceted approach. By understanding the various types of corrosion, selecting appropriate materials and protective treatments, and implementing smart design considerations, the lifespan and reliability of fasteners can be significantly enhanced.
Maintenance Strategies to Extend Fastener Life
Proper maintenance is essential to ensure the longevity and performance of fasteners in outdoor or marine environments. Implementing a comprehensive maintenance strategy can significantly reduce the risk of corrosion and extend the lifespan of these crucial components.
Regular Inspection Schedules
Regular inspections are vital to identify early signs of corrosion and address them promptly. Setting up an inspection schedule based on the environmental conditions and the criticality of the application helps in timely detection. During these inspections, it’s crucial to check for signs of rust, pitting, or any changes in the structural integrity of the fastener. Furthermore, maintaining detailed records of inspections will help in tracking the condition over time and formulating effective maintenance plans.
Cleaning Methods for Prolonged Durability
Cleaning techniques are crucial in extending the lifespan of fasteners. Eliminating dirt, salt deposits, and other contaminants that can speed up corrosion is vital. Methods like pressure washing or using gentle detergents can efficiently clean the fasteners without inflicting harm. For heavily contaminated areas, specialized cleaning agents designed to combat corrosion should be employed. Routine cleaning helps preserve the integrity of protective coatings and the fastener material itself.
Application of Anti-Corrosion Products
Applying anti-corrosion products is a proactive measure to protect fasteners. Products like corrosion inhibitors, protective sprays, or wax coatings form a barrier that prevents moisture and corrosive elements from reaching the metal surface. These treatments should be reapplied periodically, especially in harsh environments, to ensure continuous protection. Using high-quality anti-corrosion products tailored to the specific type of fastener and its environmental exposure can significantly enhance resistance to corrosion.
Innovative Solutions and Technologies in the Industry
The industry has seen remarkable advancements in materials and technologies aimed at combating corrosion in fasteners. Innovative solutions offer enhanced protection and extended life, contributing to the reliability and safety of construction projects.
Advanced Composite Materials
Advanced composite materials are being developed to replace traditional metals in fasteners, providing superior corrosion resistance. Composites such as fiber-reinforced polymers (FRP) not only resist corrosion but also offer high strength-to-weight ratios. These materials are particularly beneficial in applications where metal fasteners would corrode rapidly, such as in marine environments or chemical processing plants. By reducing the reliance on metal, composites help in sustaining the structural integrity over time.
Smart Coatings with Self-Healing Properties
Smart coatings with self-healing properties are at the forefront of innovations combating corrosion. These advanced coatings incorporate microcapsules containing healing agents, which are released when damage occurs. This process repairs minor scratches and preserves the protective barrier. Applying smart coatings to fasteners ensures that small damages do not escalate into significant corrosion problems, thereby extending service life and minimizing maintenance requirements.
Nano-Coating Technologies
Nano-coating technologies represent a breakthrough in protective treatments for fasteners. These coatings involve the application of nano-sized particles that create a superhydrophobic surface, repelling water and preventing the adherence of corrosive substances. Nano-coatings are particularly effective because they penetrate microscopic crevices and provide comprehensive protection. The thin yet durable layer formed by nano-coatings doesn’t add significant weight or alter the dimensions of the fastener, making it a practical solution for various applications.
Benefits of Addressing Corrosion Issues Proactively
Proactive measures in addressing corrosion issues for fasteners can yield numerous benefits, impacting safety, cost, and longevity positively.
Increased Safety and Structural Integrity
Ensuring that fasteners are free from corrosion directly correlates with increased safety and structural integrity. Fastening components are integral to the stability of structures, and their failure due to corrosion can lead to catastrophic results. By maintaining corrosion-free fasteners, the overall risk of structural failures diminishes, ensuring that buildings, bridges, and other constructions remain safe and reliable.
Cost Savings in Replacement and Repairs
Addressing corrosion issues proactively can lead to significant cost savings. The expenses tied to frequent replacements, extensive repairs, and potential downtimes due to corroded fasteners can accumulate substantially over time. By focusing on preventive measures such as regular inspections, appropriate material selection, and applying protective coatings, the financial burden can be mitigated. Investing in high-quality, corrosion-resistant fasteners upfront can result in reduced maintenance costs and extended intervals between replacements.
Enhanced Longevity of Construction Projects
Finally, addressing corrosion out front enhances the longevity of construction projects. Corrosion resistance contributes to the durability and resilience of structures, ensuring that they stand the test of time. Utilizing innovative materials, advanced coatings, and thorough maintenance practices enables construction projects to maintain their integrity and function over extended periods, providing long-term value and reliability.
By focusing on these maintenance strategies, innovative materials, and benefits, stakeholders can ensure that fasteners used in outdoor and marine environments remain robust, secure, and efficient, ultimately fostering safer and more durable constructions.
Qewitco‘s commitment to quality assurance is evident in their ISO 9001 certification and their thorough auditing of factories. They ensure that products are consistently of high quality and offer additional certifications such as 3.1 certification, ISIR (Initial Sample Inspection Reports), and PPAP (Production part approval process) to meet specific requirements.
Partnering with Qewitco means exceptional customer service, technical support, and access to bespoke products. They work exceptionally hard on projects to deliver the best results and provide unparalleled support throughout the process.
Choose Qewitco for all your fastening needs and experience the difference that their fine quality products and exceptional service can make. With their extensive range of fasteners, commitment to quality assurance, and customer-centric approach, Qewitco is the trusted partner you can rely on. Discover the Qewitco advantage and elevate your fastening experience today.