caTEGORIES
Tags
Deciphering the Impact of Material Choice on Bolts & Nuts in Varied Environments
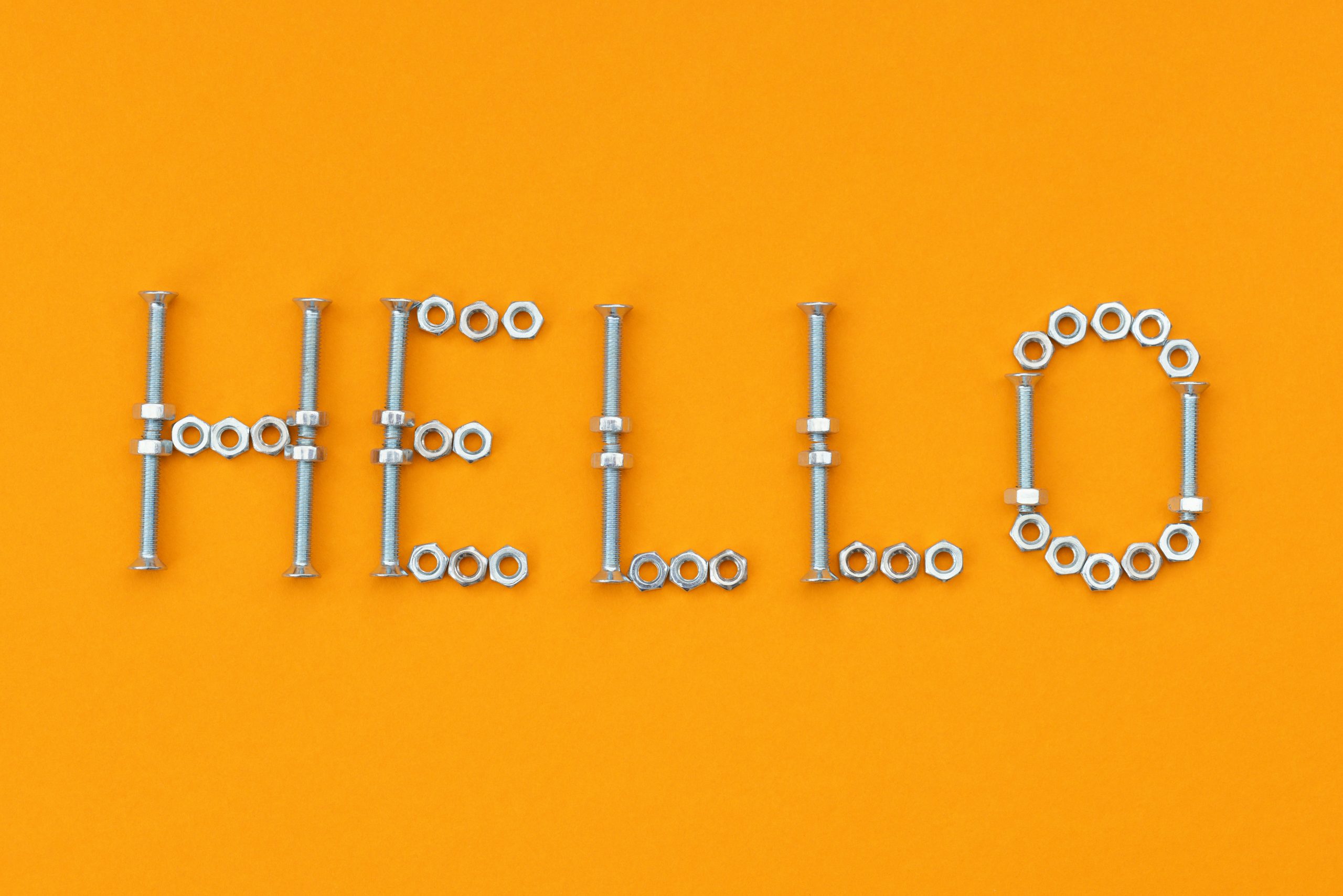
Posted: July 09, 2024
Categories: News
Tags: news
Understanding the Basics of Bolts & Nuts
Definition and Types
Bolts & nuts are fundamental fasteners used to join materials together in a non-permanent way. Bolts are externally threaded fasteners designed for insertion through holes in assembled parts, typically secured by a nut. There are various types, including hex bolts, carriage bolts, and eye bolts, each serving specific functions.
Common Applications
Bolts & nuts are utilized in numerous applications, from simple household repairs to complex industrial machinery. Their versatility makes them suitable for automotive, construction, and aerospace industries. The strength and reliability they offer are instrumental in maintaining the integrity of structures and machines.
Importance in Structural Integrity
The choice of material for bolts & nuts is critical to ensure structural integrity. These fasteners must withstand various stresses, from shear and tension to environmental factors like corrosion and temperature changes. Poor material choices can lead to fastener failure, compromising the overall safety and functionality of the assembly.
Factors Influencing Material Choice for Bolts & Nuts
Mechanical Properties
The mechanical properties, such as tensile strength, yield strength, and hardness, heavily influence the choice of material for bolts & nuts. Fasteners must be able to handle mechanical loads without deforming or breaking.
Corrosion Resistance
Corrosion resistance is vital, especially in environments prone to moisture, chemicals, or salt exposure. Materials with high corrosion resistance, such as stainless steel and certain aluminum alloys, are preferred to extend the lifespan of the fasteners.
Thermal Conductivity
Thermal conductivity impacts the performance of bolts & nuts, particularly in environments with high temperature variations. Materials with suitable thermal properties will maintain their structural integrity and performance in both high heat and cold conditions.
Popular Materials for Bolts & Nuts
Steel
Types of Steel
Steel is widely used for bolts & nuts due to its strength and durability. Carbon steel, alloy steel, and stainless steel are common variants. Each type offers different advantages regarding tensile strength and workability.
Benefits and Drawbacks
Steel fasteners are strong and relatively cost-effective. However, they can be susceptible to corrosion unless treated or alloyed with other elements like chromium to enhance resistance.
Stainless Steel
Grades of Stainless Steel
Stainless steel bolts & nuts come in various grades, such as 304 and 316. These grades differ in their composition, primarily their chromium and nickel content, which influences their performance.
Benefits and Drawbacks
Stainless steel offers excellent corrosion resistance and can withstand harsh environments. However, it is more expensive than carbon steel and may not be as strong in certain mechanical applications.
Aluminum
Properties of Aluminum
Aluminum is lightweight, corrosion-resistant, and has good thermal conductivity. It’s commonly used in applications where weight reduction is critical.
Benefits and Drawbacks
Aluminum fasteners are easy to work with and resistant to corrosion. However, their tensile strength is lower than that of steel, making them less suitable for high-stress applications.
Brass
Characteristics of Brass
Brass is a copper-zinc alloy known for its excellent corrosion resistance and conductivity. It is often used in electrical and plumbing applications.
Benefits and Drawbacks
Brass bolts & nuts are resistant to corrosion and have a pleasant appearance. However, they are softer than steel and can deform under high stress.
Performance in Different Environments
Industrial Environments
Challenges Faced
Industrial environments often involve exposure to chemicals, high stress, and varying temperatures. Fasteners in these settings must be robust and corrosion-resistant.
Suitable Materials
Stainless steel and treated steel alloys are typically suitable for industrial environments due to their strength and resistance to harsh conditions.
Marine Environments
Specific Conditions
Marine environments expose fasteners to high levels of humidity, salt, and varying temperatures, leading to aggressive corrosion.
Recommended Materials
Stainless steel, particularly grades like 316, is recommended for marine applications due to its high resistance to saltwater corrosion.
High-Temperature Environments
Material Behavior Under Heat Stress
High temperatures can weaken materials, causing them to lose strength and become brittle.
Optimal Material Choices
In high-temperature environments, materials like Inconel and stainless steel are optimal due to their ability to maintain strength and resist oxidation under heat stress.
Comparison of Material Performance Metrics
Tensile Strength Comparison
When comparing tensile strength, steel often surpasses aluminum and brass, with stainless steel providing a balance of strength and corrosion resistance.
Fatigue Resistance Analysis
Fatigue resistance is crucial for materials subjected to cyclic loads. Stainless steel and alloy steel typically offer higher fatigue resistance compared to aluminum and brass.
Corrosion Resistance Rating
Stainless steel, especially grades like 304 and 316, excels in corrosion resistance, making it suitable for harsh environments compared to plain carbon steel and aluminum.
Economic Considerations in Material Choice
Cost vs. Durability Analysis
The initial cost of materials like carbon steel is lower than stainless steel or specialty alloys. However, higher upfront costs for corrosion-resistant materials can result in long-term savings due to reduced maintenance and replacement needs.
Maintenance and Replacement Costs
Regular maintenance and replacement costs for less durable materials can add up over time. Investing in high-quality materials can mitigate these expenses.
Regulatory and Safety Standards for Bolts & Nuts in Varied Conditions
Overview of Industry Standards
Industry standards such as ASTM, ISO, and DIN provide guidelines to ensure the quality and safety of bolts & nuts. These standards cover material properties, manufacturing processes, and performance specifications.
Compliance Requirements
Manufacturers and users must adhere to these standards to ensure that fasteners perform reliably under specified conditions and meet safety regulations.
Expert Recommendations for Selecting Bolt & Nut Materials
Guidelines for Different Applications
Experts recommend selecting materials based on application-specific requirements, such as load conditions, environmental exposure, and maintenance capabilities.
Future Trends in Material Development
Future trends may include the development of new alloys and composite materials designed to further enhance the performance and longevity of bolts & nuts in challenging environments.
Qewit
Established in April 2004, Qewit has carved a niche for itself as a premier supplier of industrial consumable products, particularly fasteners, sourced from mainland China and its neighboring countries, including Taiwan, Malaysia, Vietnam, and Thailand. The company’s operations are deeply influenced by its British ownership, which has instilled a robust framework of Supply Chain Management principles that ensure the highest standards of quality and efficiency.
Understanding the nuances of material properties and their interaction with environmental factors is essential for ensuring the longevity and reliability of fasteners. Qewit‘s expertise in this domain is unparalleled, providing clients with tailored solutions that address specific challenges posed by different operational conditions. Whether it’s corrosion resistance, tensile strength, or thermal stability, Qewit’s product offerings are designed to excel in the most demanding environments.
In the broader discussion of material choice and its impact on fasteners, Qewit’s role as a trusted supplier cannot be overstated. Their comprehensive approach to supply chain management, combined with a deep understanding of material science, positions them as an invaluable partner for industries seeking reliable and high-performance fastening solutions.