caTEGORIES
Tags
Understanding the Versatility of Socket Screws in Modern Applications
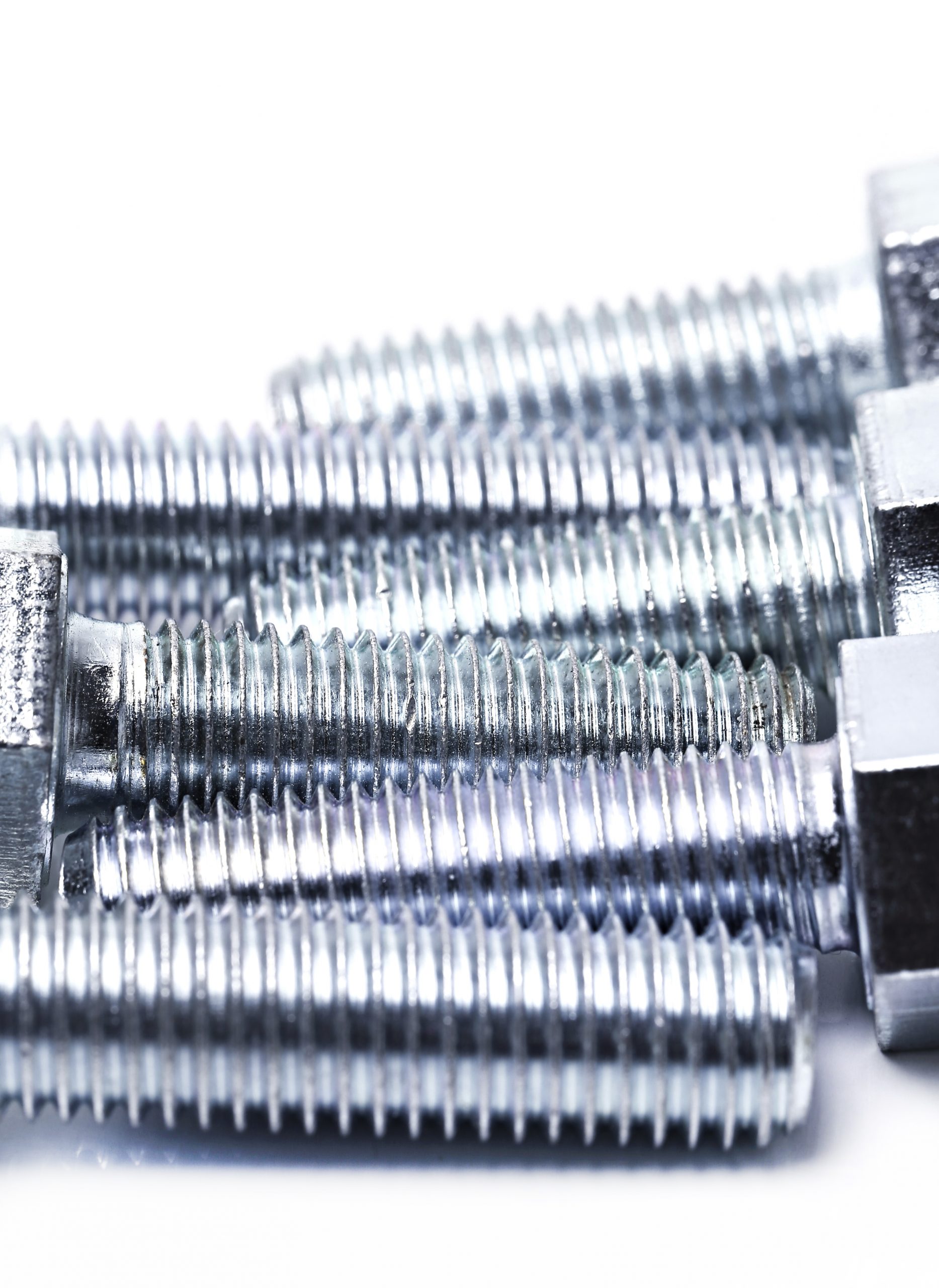
Posted: January 09, 2025
Categories: News
Socket screws have a history of progress and innovation to adapt to the needs of contemporary industries over time. They have developed alongside improvements in materials and manufacturing methods to become a staple in sectors that prioritize safety and dependability. Important design aspects include the socket for accurate torque application and different styles, like button head and flat head choices.
The Evolution and Design of Socket Screws
Historical Development of Socket Screws
Socket screws have played a role in the world of fastening technology for many years now. Their roots can be linked back to the 1900s when industries needed more dependable and effective ways to secure materials in place. Engineers were looking for a type of fastener that could handle higher levels of torque and distribute loads more efficiently than traditional options. This quest led to the creation of socket screws, with a socket design that improved accuracy during installation processes.
As time passed by, socket screws have developed along with improvements in materials and manufacturing methods. The utilization of alloy steels and surface treatments has improved their durability and resistance to rust, rendering them ideal for challenging conditions. This design has become a staple in sectors that prioritize safety and dependability cementing their importance in engineering practices.
Key Design Features and Innovations
Socket screws stand out with their design features. The hexagonal socket allows for the use of Allen keys or hex wrenches for torque application, without harming the screw head. This characteristic reduces the likelihood of stripping during installation or removal.
Socket screws have evolved with designs such as button heads and flat heads to suit various uses alongside countersunk options for a variety of applications. Coatings, like zinc plating or black oxide not enhance corrosion resistance but also add to the visual appeal of these screws. These improvements have made socket screws essential in both ornamental settings.
Diverse Applications of Socket Screws in Various Industries
Automotive Industry Utilization
The automotive industry heavily depends on socket screws because of their strength and versatility which are crucial for putting together engine parts and chassis structures as well as interior fittings in vehicles.
Safety and Performance Enhancements
Safety is important in vehicles where socket screws play a crucial role in maintaining structural integrity by securely fastening essential components even under high-stress situations. They are designed to withstand loads which guarantees reliable performance over time and minimizes the risk of mechanical breakdowns.
Aerospace Engineering Applications
In the field of aerospace, there is a need for components that can endure harsh conditions where socket screws play a vital role for their dependable nature and lightweight characteristics.
Aircraft Structural Integrity
Building airplanes requires following safety guidelines in place to ensure passenger safety at all times. Socket screws play a role in attaching various parts of the aircraft such as fuselage panels and wing assemblies along with avionic systems. Their durable nature guarantees that important connections stay secure while the aircraft is navigating through pressure changes during flight.
Advantages of Using Socket Screws in Modern Manufacturing
Enhanced Durability and Reliability
Socket screws are known for their durability due to the high-quality materials used in their production process. They can withstand strain and remain resilient against wear and tear over time, making them perfect for extended periods of use.
Resistance to Environmental Factors
Socket screws made today are built to endure environmental conditions like moisture and changes in temperature and exposure to chemicals. This durability helps them last longer and perform reliably in situations.
Ease of Installation and Maintenance
The hexagonal cutout makes it easy to install using tools, which helps prevent slipping and lowers labor expenses during assembly tasks.
If you’re looking for top-quality socket screws specifically made for industrial use cases, QEWIT provides a selection that meets strict industry standards. Their products blend cutting-edge engineering with dependable performance, offering solutions that you can rely on for your tasks.
Maintaining equipment becomes easier with socket screws since they can be removed or adjusted without causing harm to materials, making them particularly beneficial in industries that often require servicing or upgrading their equipment.
Socket screws remain an element in various industries because of their advanced design characteristics that offer flexibility and unparalleled dependability. Combining these fasteners into your endeavors guarantees top-notch functionality. Maximizes productivity throughout all production phases.
QEWIT’s Contribution to Socket Screw Advancements
Innovative Product Offerings by QEWIT
QEWIT has established itself as a player in manufacturing socket screws by offering inventive solutions that cater to the changing needs of contemporary industries. They are known for their ability to merge engineering with state-of-the-art production methods to create products that outperform functionality and dependability. With an emphasis on accuracy and longevity, QEWIT guarantees that their socket screws meet the standards set by a wide range of uses.
QEWIT offers a variety of socket screws designed to meet the requirements of different industries. Whether you need durable fasteners for heavy machinery or lighter options for aerospace use, their product range caters to various needs, with quality materials and advanced coatings that improve durability and performance.
Looking for fastening solutions? QEWIT is known for its custom-designed options that address operational needs effectively. This adaptability helps businesses enhance their operations without compromising safety or quality standards. Check out the solutions at QEWIT and see how they can add value to your projects.
Case Examples of QEWIT’s Impact on Industry Standards
The socket screws from QEWIT have established standards in various industries because of their outstanding quality and versatility. They have transformed assembly processes in the sector by guaranteeing secure connections even in high torque settings. Likewise in aerospace engineering QEWIT’s offerings have enhanced structural stability by meeting strict safety standards.
In the realm of electronics production, small socket screws play a role in assembling tiny gadgets with both accuracy and durability. Moreover, QEWIT’s durable fasteners are widely utilized in the construction industry to ensure the stability of infrastructure projects. These instances showcase how QEWIT persists in setting benchmarks for innovation and quality across various sectors.
Future Trends and Developments in Socket Screw Technology
Emerging Materials and Coatings
Innovations in materials science are leading to the development of socket screws that have improved characteristics for the future generation of products. Exciting alloys like titanium aluminum blends are becoming popular because of their strength-to-weight ratio making them ideal for industries, such as aerospace and automotive that require lightweight components.
Advancements in coating technologies are progressing well; nanocoatings are now providing exceptional levels of protection against corrosion and wear like never before seen in the industry of socket screws maintenance and performance enhancement even in extreme environmental circumstances, which is a significant advantage for businesses situated in challenging conditions; embracing these cutting edge materials and coatings could truly revolutionize their operations.
Smart Manufacturing Processes and Automation
The incorporation of manufacturing techniques is changing the way socket screws are made and used, with automated systems like robotic assembly, ensuring quality remains consistent by reducing human errors in production, a crucial factor, for industries that rely heavily upon top-notch fasteners.
Additionally, advancements in 3D printing are enabling the rapid prototyping of custom-designed socket screws, reducing lead times while maintaining accuracy. Smart sensors embedded in manufacturing equipment facilitate real-time monitoring, ensuring optimal production efficiency.
By leveraging these technological advancements, manufacturers can achieve greater scalability while maintaining adherence to strict quality standards. Socket screw technology is poised for significant evolution as industries continue to adopt smarter and more efficient production methodologies.