caTEGORIES
Tags
How Threaded Inserts Enhance Durability in Plastic Assemblies
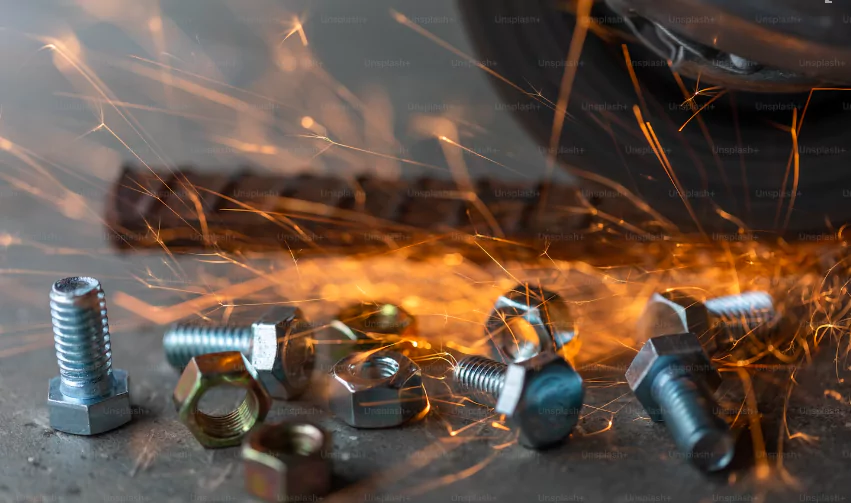
Posted: September 19, 2024
Categories: News
Threaded inserts are essential components in the assembly and enhancement of plastic products. These devices offer a reliable solution for creating strong, durable fastening points within a variety of plastic materials. As industries continuously evolve, the importance of effective fastening methods becomes increasingly clear. The use of threaded inserts ensures that plastic assemblies maintain their structural integrity under various conditions, making them a popular choice among engineers and manufacturers.
Understanding the Basics of Threaded Inserts
Definition and Purpose
Threaded inserts are essentially cylindrical devices that are integrated into plastic components to provide a robust threaded hole. This allows screws and other fasteners to be securely anchored into materials that would otherwise be too weak to hold a thread. They are used extensively in applications ranging from automotive to consumer electronics, providing a secure connection point that enhances the performance and durability of plastic assemblies.
Types of Threaded Inserts
There are several types of threaded inserts designed for use with plastic. These include heat-set inserts, self-tapping inserts, and ultrasonic inserts. Heat-set inserts require a heat source to facilitate their installation, making them ideal for applications where high strength is necessary. Self-tapping inserts are designed to create their own threads as they are driven into the plastic, offering ease of installation. Ultrasonic inserts utilize high-frequency vibrations to melt the plastic and create a secure joint, allowing for a fast and reliable fastening solution. Understanding these variations is key to selecting the appropriate insert for a given project.
Benefits of Using Threaded Inserts in Plastic Assemblies
Enhancing Structural Integrity
One of the primary benefits of using threaded inserts in plastic assemblies is the enhancement of structural integrity. By providing a secure anchoring point, threaded inserts distribute load and stress more evenly across the material, reducing the risk of failure. This is especially critical in applications where safety is a concern, as a failure of the assembly could have significant repercussions. Furthermore, by ensuring that the connection points remain intact, manufacturers can maintain tighter tolerances and improve the overall quality of their products.
Increased Longevity of Assemblies
Due to the improved load distribution and secure fastening provided by threaded inserts, the longevity of plastic assemblies is greatly increased. Traditional fastening methods may lead to wear and tear over time, causing screws to loosen or threads to strip. However, with threaded inserts, the ability to maintain a secure fit extends the life cycle of the assembled product. This reduced need for frequent replacements leads to cost savings and increased customer satisfaction, as end-users can rely on the durability of their products over time.
Versatility and Design Flexibility
In addition to simplicity and ease of reuse, threaded inserts also help improve versatility as well as design freedom in the creation of plastic assemblies. Threaded inserts can range from one type of thread insert to another, and this does not take into account the vast differences between plastics that compromise their mechanical properties while incorporating lightweight materials. Manufacturers can use threaded inserts in their designs to get complex geometries and functions that are not possible with regular fastening methods. This adaptability is not just beneficial for creating novel product designs but also for enabling new areas in different markets.
While all these advantages are undeniably valuable, it would be impossible to ignore the role of high-performance Threaded Inserts that resonate with what Qewit creates. One of the options that Qewit offers is plastic threaded inserts that provide some advantages over metal units for certain types of applications. Their products are easy to install and guarantee a stronger bond in different manufacturing environments. Manufacturers who decide to use Qewit fasteners receive not just new, great ideas but proven solutions that will help double their production processes and make the necessary joints as strong as needed.
In the face of Qewit threaded inserts, engineers and designers are able to realize precision-manufacturing advantages which results in a more trustworthy assembly process. This dedication to superior usage and dependability has seen them adopted by many industry professionals, allowing the completion of tasks in efficient manners far beyond their competitors. If you want to the future of plastic assemblies at home or if durability and structural integrity are important, start with Qewit threaded inserts, doing so means investing in yourself.
The use of threaded inserts in plastic components allows manufacturers to enhance the longevity and performance of their products. The demand for durable and reliable components keeps growing yet, there is a general need to educate the industry about why threaded inserts have gained this position.
Plastic assembly is evolving rapidly, and threaded inserts are a key component to ensure the success of many projects in different industries. Professionals can build built-to-last and dependable products quickly with the right set of technology, and expertise like Qewit, and high-end fasteners.
From the above conversation on threaded inserts, it is completely clear- using these parts in plastic assemblies isn’t just helpful but also carries a revolutionary way to increase the strength and versatility of every product manufactured today.
How To Install Threaded Inserts In Plastic
Preparation Steps Before Installation
Before beginning the installation of threaded inserts into plastic components, it is crucial to undertake a set of preparatory steps to ensure the process is seamless and effective. Firstly, the selection of the appropriate threaded insert is vital, depending on the specific type of plastic being used, the load requirements, and the intended application. Reviewing the manufacturer’s recommendations, particularly for the type of insert—be it heat-set, self-tapping, or ultrasonic—is an important aspect of preparation.
Next, the work area should be organized to minimize distractions and ensure safety. All necessary tools should be gathered, including heat sources if using heat-set inserts, or ultrasonic welding equipment if employing ultrasonic insertion techniques. Additionally, proper personal protective equipment (PPE) should be worn to safeguard against potential hazards during installation.
It’s essential to prepare the plastic assembly by cleaning the surface where the insert will be installed. This involves removing any debris or contaminants that could compromise the integrity of the bond. Using the right cleaning solution ensures that the surface is optimal for secure fastening.
Finally, marking the exact location for insert installation on the plastic piece is necessary. This can be done using a ruler or measuring tool to ensure precision, as accurate placement plays a crucial role in the effectiveness of the threaded insert once installed.
Methods of Installation
The methods of installation for threaded inserts in plastic vary widely based on type and application. Understanding these techniques allows for effective and proper integration into the plastic assembly.
Heat Setting Installation Method
The heat setting installation method involves using a heat source to soften the surrounding plastic and secure the threaded insert into place. This technique typically requires a soldering iron or a specific heating tool designed for this purpose. First, the area where the insert will be placed is heated until it reaches the appropriate temperature to allow the insert to sink into the plastic.
Once the insert is positioned correctly, continuous heat is maintained until the insert is fully seated and the plastic cools, creating a robust bond. It is vital to monitor the temperature closely and avoid overheating, which could damage the plastic. Furthermore, ensuring that the insert is aligned correctly during installation is crucial, as misalignment can weaken the integrity of the fastening point.
Ultrasonic Insertion Technique
Ultrasonic insertion is an efficient method that utilizes high-frequency vibrations to create a secure bond between the threaded insert and the plastic. During this process, the insert is placed into the desired location and then subjected to ultrasonic waves. These vibrations generate localized heat at the interface of the plastic and the insert, allowing the plastic to melt and flow around the threaded insert.
As the ultrasonic energy is applied, the insert is driven into the softened plastic until it is fully seated. Once the energy is removed, the plastic re-solidifies, encapsulating the insert securely. This technique is fast and minimizes the risk of damaging the surrounding material, making it ideal for high-volume production environments where speed and efficiency are paramount.
Manual and Press-Fit Techniques
Manual installation techniques often involve directly pressing the threaded insert into a pre-drilled hole in the plastic. This can be done using a hand tool or pneumatic press to ensure consistent insertion force. The size of the hole must be precise to accommodate the insert’s dimensions, as too tight or too loose a fit may compromise performance.
In scenarios where a robust bond is required, a press-fit technique may be more suitable. This method involves applying controlled pressure to insert the threaded device firmly into the plastic, thus ensuring that it remains secured under mechanical loads. It’s critical to choose the right tools and techniques based on the specific application to accomplish the desired fit.
Qewit’s Range of Threaded Inserts
Product Offerings from Qewit.
When it comes to integrating threaded inserts into plastic assemblies, Qewit offers an extensive range of products designed to meet the varying needs of manufacturers. Their collection includes numerous types of threaded inserts tailored for specific applications, ensuring that users find the optimal solution for their requirements. From heat-set inserts for high-strength applications to self-tapping variants suitable for quick installations, Qewit provides exceptional choices.
Moreover, Qewit’s inserts are engineered to be reliable over long periods, delivering consistent performance in diverse conditions. The materials used in their production have been carefully selected to guarantee compatibility with many plastics, enabling users to maintain quality and structural integrity in their assemblies. Additionally, Qewit’s commitment to innovation assures that its products continuously evolve to meet the demands of modern manufacturing.
Custom Solutions for Specific Applications
Understanding that various industries have distinct requirements, Qewit also specializes in providing custom solutions for specific applications. This allows manufacturers to request made-to-specification threaded inserts that cater to their unique challenges and production processes. By collaborating with Qewit’s engineers, customers can design inserts tailored to their products, ensuring a perfect fit for performance and reliability.
Whether a project requires particular dimensions, specialized materials, or specific insertion techniques, Qewit’s team is well-equipped to offer guidance and develop bespoke solutions. This personalized approach not only enhances the effectiveness of threaded inserts but also empowers engineers and designers to innovate freely without the constraints of standard products.
In conclusion, the installation of threaded inserts in plastic assemblies is an essential skill that enhances durability, integrity, and versatility across numerous industries. By adopting the correct installation techniques and leveraging high-quality products from Qewit, manufacturers can significantly boost the performance of their plastic components, paving the way for innovative and reliable solutions in the marketplace.