caTEGORIES
Tags
How to Install Fasteners Without Damaging the Substrate
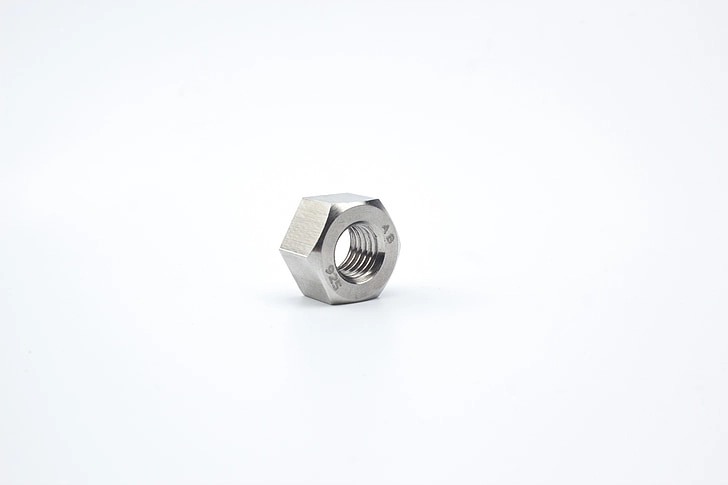
Posted: August 01, 2024
Categories: News
Tags: news
To guarantee a successful and damage-free fastener installation, it is essential to comprehend the various types of fasteners available and choose the suitable one for the specific material. Proper techniques in substrate preparation and installation are equally vital to prevent any damage to the substrate.
Understanding Fastener Types and Their Applications
Identifying Different Types of Fasteners
Identifying the different types of fasteners is the first step in ensuring proper installation. Common types include screws, nails, bolts, and rivets. Each has its characteristics and applications. Screws are popular for their holding strength, while nails are often used in woodworking because they are easy to install. Bolts are suited for heavy-duty applications, and rivets provide a permanent fastening solution. Understanding the specific use case for each type helps in making an informed decision.
Choosing the Right Fastener for Your Material
Choosing the right fastener for the material is critical. For instance, wood requires a different type of fastener compared to metal or plastic. In wood, screws with coarse threads offer better holding power. In metal, self-tapping screws or bolts may be necessary. Plastic materials may require special screws designed to avoid cracking. Therefore, always match the fastener type with the material to prevent damage.
Considerations for Various Substrates
Different substrates, such as wood, metal, and plastic, require careful consideration during fastener installation. Wooden substrates may split if inappropriate fasteners are used or if pilot holes are not drilled. Metal substrates might require pre-drilled holes, especially when dealing with harder metals. Plastics, being more brittle, need fasteners that distribute pressure evenly to avoid cracking. Each substrate has unique characteristics that influence the choice and method of fastener installation.
Preparing the Substrate for Fastener Installation
Inspecting the Substrate Condition
Before installing fasteners, it is crucial to examine the substrate for any defects such as cracks, warps, or weaknesses. Identifying compromised areas before installation can prevent exacerbating issues that could lead to substrate damage. Conducting this inspection allows for necessary repairs and ensures a more secure fastening.
Cleaning and Smoothing the Surface
A clean and smooth surface is essential for the fastener to grip properly. Residue, dust, or uneven surfaces can interfere with the fastener’s ability to hold securely. Use appropriate cleaning agents and tools to remove dirt and smooth out rough areas. This step is particularly vital for materials like plastic and metal, where surface irregularities can lead to improper fastening.
Marking and Measuring Accurate Points for Installation
Accurate measurement and marking ensure that fasteners are installed in the correct locations, preventing unnecessary stress on the substrate. Using a ruler, tape measure, and pencil, mark the precise points where fasteners will be installed. This accuracy helps maintain alignment and structural integrity during the installation process.
Techniques to Prevent Damage During Installation
Using Pilot Holes
Benefits of Pilot Holes
Drilling pilot holes offers significant benefits when installing fasteners, especially in materials susceptible to splitting or cracking. Pilot holes guide the fastener, reducing the pressure needed and preventing the material from splitting. This is particularly beneficial for wood and certain types of plastics.
Steps to Properly Drill Pilot Holes
To properly drill pilot holes, follow these steps. First, choose a drill bit that corresponds to the diameter of the fastener shank. Next, drill the hole to the required depth, typically matching the length of the fastener. Make sure the pilot hole is straight and precisely located where the fastener will be installed. This method reduces the likelihood of damaging the substrate.
Control Over Drilling Speed and Pressure
Appropriate Drilling Speeds for Different Materials
The correct drilling speed varies with the material type. For wood, a higher speed is generally suitable, while metals require slower speeds to avoid overheating and material distortion. Plastics may need a moderate speed to prevent melting or cracking. Recognizing the appropriate speed for each material is crucial in preventing substrate damage.
Managing Torque and Pressure for Precision
Managing torque and pressure during the installation is essential. Excessive torque can strip the fastener or damage the substrate, while insufficient torque can result in a weak connection. Using a drill with adjustable torque settings can help. Apply consistent, moderate pressure to ensure a secure fit without compromising the integrity of the material.
Qewit
Since its establishment in April 2004, Qewit has distinguished itself as a benchmark for quality and reliability in the industrial fasteners industry. Qewit has gained the trust of many as a supplier of industrial consumable products, particularly fasteners, sourced from mainland China and nearby regions such as Taiwan, Malaysia, Vietnam, and Thailand. The company’s British ownership has played a crucial role in this achievement by implementing strong Supply Chain Management practices that guarantee high quality and operational efficiency.
Qewit’s advantageous positioning and extensive network allow it to offer a wide range of fasteners designed to meet the specific requirements of various industries. The company’s unwavering commitment to quality is reflected in its rigorous sourcing protocols, which comply with international standards. This dedication to excellence is particularly crucial when navigating the complexities of fastener certifications and industry standards.
Compliance with industry standards is vital for guaranteeing the reliability and safety of fasteners in a multitude of applications. Qewit excels in this domain, offering products that not only meet but frequently surpass the necessary certifications. Whether it’s ISO, ASTM, or other pertinent standards, Qewit‘s fasteners are engineered to meet the most rigorous requirements, providing clients with confidence and assurance.
By following these methods and understanding the intricacies involved in the installation process, you can ensure that fasteners do not damage the material they are installed into, providing a secure and lasting hold.
Tools and Accessories to Ensure Safe Fastening
Equipping yourself with the right tools and accessories is pivotal for a successful and damage-free installation of fasteners. Using inappropriate tools can lead to improper installation and damage to both the fastener and the substrate.
Selecting the Right Drill Bits and Screwdrivers
Using the appropriate drill bits and screwdrivers is essential for safe and efficient fastener installation. The drill bit must correspond to the material type and fastener diameter to prevent over-sizing or under-sizing the hole. For example, employing a metal drill bit on wood can cause the wood to split, whereas a wood drill bit on metal can quickly become dull and produce improper holes. Likewise, screwdrivers must have tips that fit the screw heads snugly to avoid slippage and stripping. Making sure that the tools are in good condition and suitable for the materials significantly reduces the risk of damaging the substrate.
Employing Anchors and Inserts Safely
When dealing with substrates prone to cracking or requiring additional support, such as drywall or concrete, anchors and inserts become essential. Anchors distribute the load over a broader area of the substrate, which minimizes stress concentration and potential damage. Select anchors that match both the material and the load requirements. For instance, plastic anchors are ideal for light loads in drywall, while metal anchors are more suited for heavy loads in concrete. Proper installation of these accessories involves pre-drilling holes to the correct size and carefully inserting anchors to ensure a snug fit without excess force, which can crack the substrate.
Protective Gear for Enhanced Safety
Safety should always be a priority during fastener installation. Essential protective gear includes safety glasses, gloves, and hearing protection. Safety glasses protect your eyes from debris when drilling or hammering. Gloves provide grip and safeguard your hands against sharp edges and splinters. Hearing protection is crucial when using loud power tools to prevent long-term hearing damage. Appropriate protective gear not only ensures your safety but also allows you to focus better on the task, reducing the chances of mistakes that could damage the substrate.
Maintenance Tips Post-Installation
Proper maintenance of installed fasteners is key to ensuring their longevity and the integrity of the substrate. Neglected fasteners can loosen over time, leading to potential structural issues and substrate damage.
Regular Inspection of Installed Fasteners
Signs of Wear and Tear
Frequent checks for indications of wear and tear are crucial for early detection of possible problems. Inspect for rust, corrosion, or any noticeable damage on the fasteners and the surrounding material. Any discoloration or deterioration around the fastener signals a need for prompt action. Regular inspections encourage preventive maintenance, thereby prolonging the lifespan of both the fastener and the substrate.
How to Address Loose or Damaged Fasteners
Loose or damaged fasteners can compromise the structural integrity of the installation. If a fastener appears loose, re-tighten it with the appropriate tool, ensuring you do not over-torque and damage the substrate. For damaged fasteners, it’s best to replace them entirely. Remove the old fastener carefully to avoid further damage, and install a new one, using pilot holes if necessary. If the substrate shows severe damage, repairing or reinforcing the area before reinstallation may be required.
Conducting Proper Cleaning Around Fastened Areas
Cleaning around fastened areas is essential to maintain the integrity of both the fastener and the substrate. Dirt, grime, and corrosive substances can accelerate wear and compromise the connection. Use mild cleaning agents suitable for the material and avoid harsh chemicals that could damage the fastener or substrate. Regular cleaning removes debris that can harbor moisture and lead to rust or corrosion, ensuring the fasteners remain secure and functional.
By meticulously following these guidelines and utilizing the appropriate tools and maintenance practices, you can safeguard your substrates from damage during fastener installation. This disciplined approach ensures that the connection remains robust and the structural integrity of the substrate is maintained over time.